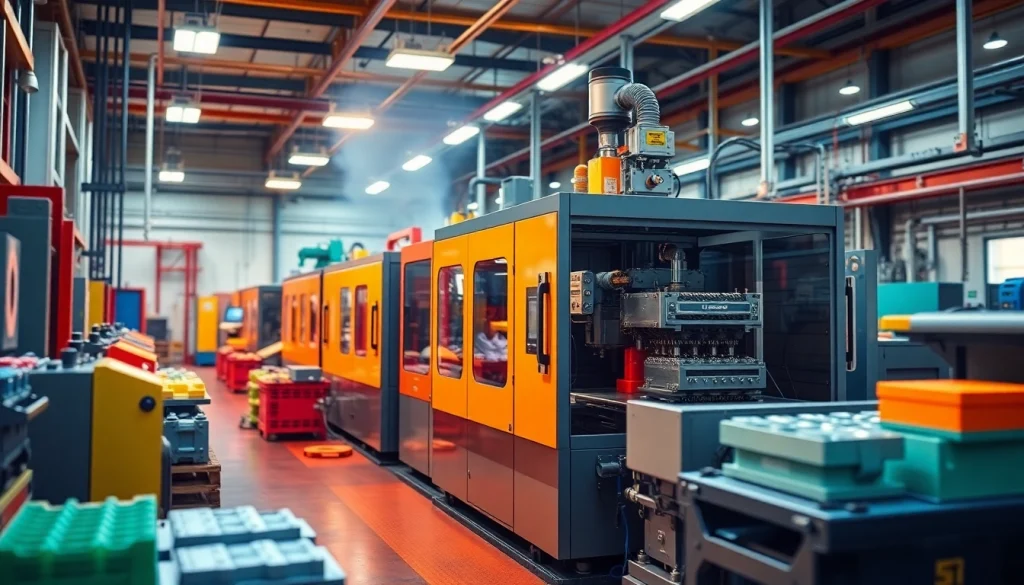
Introduction to Injection Molding
Injection molding is a highly efficient manufacturing process that plays a crucial role in the production of plastic parts and components. By injecting molten material into a mold, manufacturers can create complex and precise shapes that are essential for a variety of applications in numerous industries. This process not only allows for high-volume production but also offers flexibility in design and materials. As we delve deeper into the intricacies of injection molding, we will explore its definition, historical evolution, and wide-ranging applications.
What is Injection Molding?
Injection molding is a manufacturing technique wherein molten plastic is injected into a mold cavity to produce parts that solidify into the desired form. The process begins with the melting of plastic pellets, which are then injected under high pressure into the mold, where they take shape as they cool and harden. This approach is suitable for mass production of identical parts, making it one of the most common methods for creating plastic products.
The History of Injection Molding
The origins of injection molding can be traced back to the early 19th century. The earliest known patent for an injection molding machine was issued to John Wesley Hyatt in 1872. Hyatt’s innovation allowed for the first mass-production of celluloid combs, marking a significant advancement in manufacturing. As plastics became more widely available in the mid-20th century, injection molding gained popularity and evolved with the introduction of new materials and technologies, enabling the production of more complex and higher quality parts.
Applications of Injection Molding
Injection molding is utilized across a plethora of industries, including:
- Automotive: Components such as dashboards, bumpers, and interior fittings.
- Consumer Electronics: Casings and internal components for smartphones, laptops, and other devices.
- Medical Devices: Syringes, housings for equipment, and various components that require precision engineering.
- Household Goods: Items like food containers, toys, and furniture parts.
The Injection Molding Process Explained
Stages of the Injection Molding Process
The injection molding process comprises several distinct stages, each critical to producing high-quality molded parts. These stages include:
- Clamping: The mold is securely closed to contain the injected material.
- Injection: Molten plastic is injected into the mold cavity at high pressure.
- Cooling: The plastic is allowed to cool and solidify within the mold, taking its shape.
- Ejection: Once cooled, the mold opens and ejects the finished product.
Materials Used in Injection Molding
Various materials are utilized in injection molding, with the most common being thermoplastics, thermosetting plastics, and elastomers. Each material offers unique properties, making it suitable for different applications:
- Thermoplastics: Materials like polypropylene and polycarbonate that can be remelted and reshaped.
- Thermosetting Plastics: Materials that harden permanently after being shaped, such as epoxy and phenolic resins.
- Elastomers: Flexible materials that can handle deformation, perfect for applications requiring elasticity.
Technical Specifications of Injection Molding Machines
An injection molding machine consists of several key components:
- The Injection Unit: Melts and injects the plastic into the mold.
- The Clamping Unit: Holds the mold closed during injection and opens it for ejection.
- The Control System: Manages the parameters of the injection molding cycle, including temperature and pressure settings.
Modern machines are equipped with computerized controls that optimize performance and minimize waste.
Advantages of Injection Molding
Cost Efficiency in Production
One of the most significant advantages of injection molding is its cost-efficiency, particularly for large production runs. The initial setup cost for the molds is high; however, the long-term benefits include:
- Reduced labor costs due to automation.
- Lower material waste compared to other manufacturing processes.
- High output rates with consistent quality in each production cycle.
Design Flexibility and Precision
Injection molding offers remarkable design flexibility and the ability to achieve intricate geometries and high tolerances. With advancements in mold-making technologies, designers can create complex shapes that would be challenging or impossible with alternative manufacturing methods.
Benefits for Mass Production
This manufacturing technique is ideally suited for mass production, where the same part can be produced repeatedly with minimal variations. As a result, injection molding allows companies to meet large-scale demand efficiently, facilitating economies of scale and quicker market entry for new products.
Common Challenges in Injection Molding
Defects in Injection Molding
Despite its advantages, injection molding is not without challenges. Common defects include:
- Warpage: Distortion due to uneven cooling.
- Short Shots: Incomplete filling of the mold cavity.
- Flash: Excess material that forms around the edges of molded parts.
Identifying and addressing these defects promptly can significantly improve product quality.
Management of Cycle Times
Managing cycle times is critical for optimizing productivity. Various factors, including material properties, mold design, and machine performance, influence cycle time. Automation and advanced robotics can enhance speed and precision, further improving overall efficiency.
Material Selection Challenges
Selecting the right material for injection molding is crucial. Factors such as the part’s intended use, environmental conditions, and desired physical characteristics must be considered. Collaborating closely with material suppliers can help manufacturers make informed decisions, avoiding costly mistakes.
The Future of Injection Molding
Trends in Injection Molding Technology
The injection molding landscape is continuously evolving. Current trends include:
- Industry 4.0: Integration of IoT and smart technology for real-time monitoring and data analysis.
- Advanced Materials: Development of new materials that enhance performance while being environmentally friendly.
- Rapid Prototyping: The ability to quickly produce prototypes to facilitate design iterations and testing.
Innovative Materials in Injection Molding
Research and development in materials science are leading to the introduction of innovative plastics and composites that provide improved mechanical properties and sustainability. For example, biodegradable plastics are being developed for applications where environmental impact is a concern.
Sustainable Practices in Injection Molding
As companies strive for sustainability, injection molding is adapting to incorporate greener practices. This includes using recycled materials, improving energy efficiency in production, and adopting eco-friendly manufacturing methods. These practices not only reduce waste but also align with consumer preferences for sustainable products.