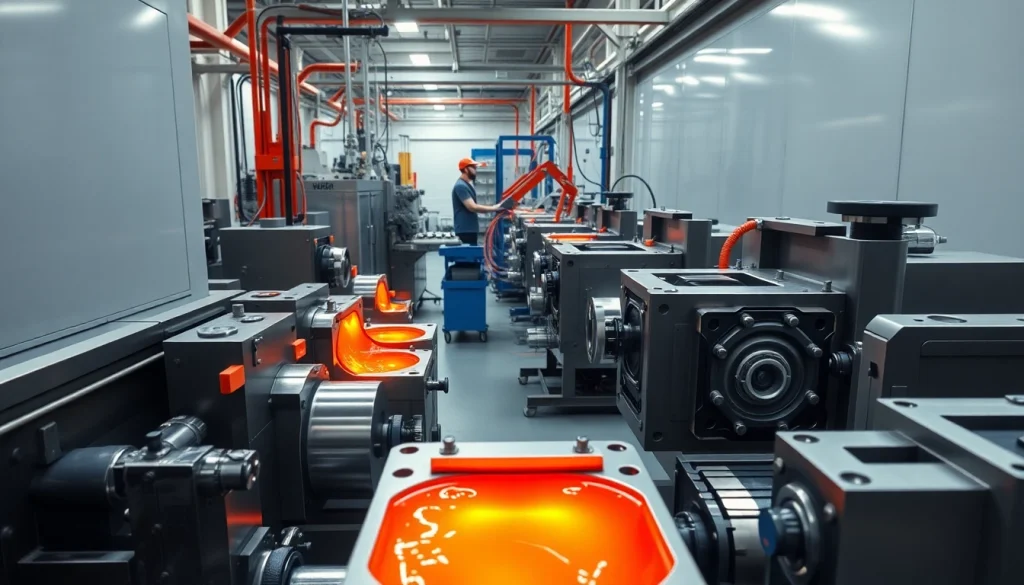
Understanding Injection Molding Fundamentals
Injection molding serves as a cornerstone of modern manufacturing, efficiently creating various plastic items through a highly controlled process. This technique involves injecting molten material into a mold to create detailed and complex shapes. Not only does it facilitate the mass production of plastic products, but it also allows for customization and precision in manufacturing. In this comprehensive guide, we will explore the intricacies of injection molding, including its defining characteristics, essential materials, and the vital role of mold design. For detailed insights into injection molding, continue reading.
What is Injection Molding?
Injection molding is a manufacturing process that produces parts by injecting molten materials—primarily plastics, but also metals and elastomers—into a pre-designed mold. This method is known for its efficiency and precision, making it ideal for mass-producing components ranging from small plastic parts to larger items like automotive body panels. Typically, the process involves several stages: heating the material until it becomes liquid, injecting it into the mold under high pressure, allowing it to cool and solidify, and finally ejecting it from the mold.
Key Materials Used in Injection Molding
The versatility of injection molding largely comes from the broad range of materials that can be utilized, including:
- Thermoplastics: These are the most commonly used materials for injection molding due to their ability to be reheated and reshaped. Examples include polypropylene, polystyrene, and polycarbonate.
- Thermosetting Plastics: Unlike thermoplastics, these materials harden permanently after being molded. Examples include epoxy resins and phenolic resins.
- Metals: Certain metals like zinc and aluminum can also be used in specialized injection molding processes known as metal injection molding (MIM).
- Elastomers: Rubber-like polymers are often used for parts that require flexibility and elasticity, such as seals and gaskets.
The Importance of Mold Design
Mold design holds significant sway over the quality and efficiency of the injection molding process. A well-designed mold accounts for factors such as:
- Uniform Pressure Distribution: This ensures that the molten material fills the mold evenly, reducing the risk of defects.
- Cooling Efficiency: Properly designed cooling channels within the mold expedite cooling and improve cycle times.
- Ease of Ejection: Consideration must be given to how parts are released from the mold to avoid damaging delicate features.
Injection Molding Process Stages
Clamping, Injection, and Cooling
The injection molding process consists of four key stages:
- Clamping: The mold is securely closed by a clamping unit to ensure it remains tightly shut during the injection process.
- Injection: Molten material is injected into the mold under high pressure, filling the cavity.
- Cooling: The material cools and solidifies, taking the shape of the mold. This stage is crucial for dimensional accuracy.
- Ejection: Once cooled, the mold opens, and the finished part is ejected.
Common Cycle Times and Efficiency
Cycle times in injection molding can vary significantly based on several factors, including the type of material, the complexity of the mold, and the size of the component. Generally, cycle times can range from 10 seconds for smaller parts to several minutes for larger, more complex items. As such, optimizing cycle time is essential for maximizing production efficiency. Techniques such as improving mold design and optimizing injection speed can significantly reduce cycle times.
Tools and Equipment in Injection Molding
The equipment utilized in injection molding includes:
- Injection Molding Machine: These machines vary in size and capacity, ranging from small bench-top models to large industrial machines capable of producing large volumes.
- Molds: Made from durable materials like steel or aluminum, molds are custom-designed for each product.
- Material Feed Systems: These systems ensure that the right amount of material is consistently fed into the injection unit.
- Cooling Systems: Integral for maintaining optimal temperature control throughout the cooling phase.
Advantages of Injection Molding
Cost-Effectiveness in Mass Production
One of the primary benefits of injection molding is its cost-effectiveness, particularly in mass production scenarios. The initial investment in molds can be high, but the cost per unit decreases significantly as production numbers increase. As small variations in production costs become negligible, businesses can achieve substantial savings when producing large quantities of identical parts.
High Precision and Repeated Quality
Injection molding is synonymous with precision. The process allows manufacturers to produce components with extremely tight tolerances, ensuring that each part meets the required specifications. This repeatability is crucial for industries where component reliability is essential, such as automotive and aerospace.
Versatility in Production
From intricate parts for consumer electronics to robust components for industrial machinery, injection molding can meet diverse production needs. The ability to use various materials and create complex geometries makes it an attractive choice across multiple applications.
Challenges and Solutions in Injection Molding
Common Injection Molding Defects
Despite its advantages, injection molding can be prone to defects. Common issues include:
- Warpage: This occurs when parts deform during the cooling process, often due to uneven cooling rates.
- Short Shots: Inadequate material injection leads to incomplete parts.
- Bubbles or Voids: These arise from trapped air during the injection process, resulting in compromised integrity.
Material and Equipment Limitations
Choosing the right material for specific applications is vital while considering properties such as melting point, viscosity, and thermal stability. Additionally, outdated or poorly maintained equipment can impact the quality and efficiency of the process. Regular equipment assessments and timely upgrades can help mitigate these risks.
Best Practices for Quality Control
Maintaining quality throughout the injection molding process involves several best practices:
- Regular Inspections: Routine checks of molds and machinery to ensure they are functioning correctly.
- Material Testing: Thoroughly testing materials before production to avoid defects caused by low-quality inputs.
- Data Analysis: Utilizing production data to identify trends and areas for improvement.
Future Trends in Injection Molding
Innovations in Materials and Processes
The injection molding industry is evolving rapidly, with advancements in materials and processes enhancing efficiency and capability. Innovations such as bio-based and recycled materials are gaining traction, reflecting a growing focus on sustainability. Furthermore, additive manufacturing techniques are being combined with traditional injection molding to create hybrid processes that leverage the strengths of both technologies.
Environmental Considerations and Sustainability
As sustainability becomes a primary concern across industries, injection molding is adapting to meet these challenges. Manufacturers are increasingly focusing on reducing waste during production, implementing recycling programs, and exploring alternative materials that minimize environmental impact. Techniques such as closed-loop systems are gaining popularity to reduce resource consumption.
Industry Demand and Market Predictions
The demand for injection molded products continues to grow, driven by sectors such as automotive, healthcare, and packaging. Market predictions indicate that the industry will see substantial growth in the coming years, particularly as technologies evolve and manufacturers seek more efficient and sustainable production methods. The combination of lower costs, improved material options, and enhanced production techniques positions injection molding as a central strategy in the manufacturing landscape.