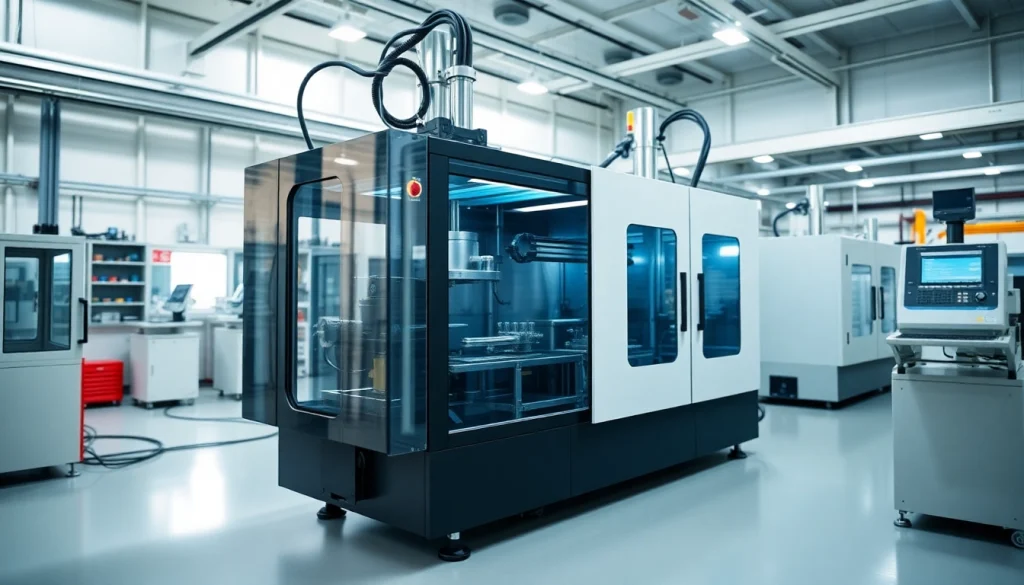
Introduction to Injection Molded Parts
Injection molded parts are a cornerstone of modern manufacturing, providing efficiency, precision, and versatility in producing a wide range of components. This production method has transformed industries by allowing the mass production of complex, high-quality parts at competitive costs. As companies increasingly seek ways to optimize production and heighten product quality, understanding injection molded parts becomes paramount, particularly for sectors like automotive, consumer goods, electronics, and healthcare. This article delves into various aspects of injection molded parts, from fundamental definitions and significant applications to key components of the manufacturing process.
What Are Injection Molded Parts?
Injection molded parts are items created through the injection molding process, where plastic material is melted and injected into a mold to form a desired shape. This manufacturing technique is ideal for producing high volumes of identical items with remarkable accuracy and surface finish. The process involves several stages: the plastic material is heated until it melts, after which it is injected into a mold under high pressure. Once the plastic cools, the mold is opened, and the solidified part is ejected. This method allows for various geometries, complex designs, and many colors or finishes, making it a popular choice across diverse applications. For a more detailed exploration of injection molded parts, you can find useful insights about their manufacturing by visiting injection molded parts.
The Importance of Injection Molding in Manufacturing
Injection molding has become a critical part of the manufacturing landscape due to its unparalleled efficiency and cost-effectiveness. Some key benefits include:
- High Production Rates: Injection molding can produce thousands of parts in a very short time, making it suitable for mass production.
- Design Flexibility: The ability to create intricate shapes yields products that meet specific industry requirements.
- Material Versatility: A wide array of thermoplastics and thermosetting materials can be used, allowing manufacturers to choose materials that best fit their application needs.
- Reduced Waste: The process is efficient, resulting in minimal waste material compared to traditional manufacturing techniques.
Consequently, understanding the importance of injection molding is crucial for businesses aiming to stay competitive in today’s fast-paced markets.
Applications of Injection Molded Parts in Various Industries
Injection molded parts serve myriad functions across industries, showcasing their versatility. Some prominent applications include:
- Automotive: Components like dashboards, bumpers, and interior parts are commonly produced using injection molding due to the material’s strength and lightweight characteristics.
- Consumer Goods: Everyday products such as kitchen utensils, packaging containers, and toys utilize injection molding for high-volume production.
- Electronics: Injection molding is used to manufacture casings, connectors, and various other electronic components, which require precision and durability.
- Healthcare: Medical devices, surgical instruments, and pharmaceutical packaging often incorporate injection molded parts for reliable performance and sterility.
The breadth of applications illustrates how vital injection molded parts are to contemporary manufacturing, accommodating diverse needs efficiently.
Components of Injection Molding Machines
Key Parts Involved in Injection Molding
Understanding the components of injection molding machines is essential for grasping how injection molded parts are produced. The primary components include:
- Injection Unit: This unit is responsible for melting and injecting the plastic into the mold. It consists of a hopper, barrel, and screw or plunger.
- Mold: The mold shapes the melted plastic into the desired part configuration. It typically comprises two halves: the cavity and the core.
- Clamping Unit: This component holds the mold in place during the injection process. It applies clamping force to keep the mold halves tightly shut while the plastic is injected.
How Each Component Contributes to the Process
Each component plays a vital role in ensuring the injection molding process’s efficiency and effectiveness:
- Injection Unit: The injection unit is essential for controlling the temperature and pressure required to melt and fluently inject plastic into the mold.
- Mold: The mold dictates the final shape and detail of the part, influencing aspects like surface finish, dimensional accuracy, and product strength.
- Clamping Unit: The clamping unit’s strength is crucial for preventing leakage of plastic during injection and ensuring the mold remains closed under high-pressure conditions.
The seamless interaction of these components enables the efficient production of high-quality injection molded parts.
Maintenance Best Practices for Injection Molding Machines
To maintain efficient operations and extend the lifespan of injection molding machines, implementing proactive maintenance measures is critical. Recommended practices include:
- Regular Inspections: Conduct routine inspections to identify wear and tear trends; this can prevent unexpected downtimes.
- Lubrication: Ensure proper lubrication of moving parts to minimize friction and reduce wear.
- Component Replacement: Timely replacement of worn-out components, such as screws or nozzles, prevents performance loss and enhances product quality.
By adhering to these maintenance best practices, manufacturers can significantly enhance the reliability and efficiency of their injection molding machines.
Designing for Injection Molded Parts
Key Design Considerations for Optimal Moldability
Design plays a critical role in the success of injection molded parts. Key considerations should focus on optimizing the design for manufacturability, including:
- Draft Angles: Incorporating draft angles allows for easier removal of the part from the mold without damaging it.
- Wall Thickness: Maintaining consistent wall thickness ensures even cooling and reduces the risk of warping or defects during solidification.
- Radii: Adding radii to corners helps distribute stress evenly throughout the part, enhancing structural integrity.
Integrating these considerations early in the design phase facilitates easier moldability and enhances the performance of the final product.
Common Challenges in Injection Mold Design
Despite its advantages, injection molding presents several design challenges that engineers must navigate:
- Sink Marks: These depressions on the surface of molded parts occur when the material shrinks during cooling. Designing with uniform wall thickness can help mitigate this issue.
- Bubbles and Voids: Air entrapment during injection can lead to defects. Proper venting and mold design can reduce these occurrences.
- Warping: Parts may warp due to uneven cooling. Ensuring consistent heating and cooling will promote dimensional stability.
Being proactive about these challenges during the design phase allows for adjustments that can lead to vastly improved outcomes during production.
Innovative Materials for Enhanced Performance
The choice of materials significantly influences the performance of injection molded parts. Engineers continuously explore innovative materials to enhance properties such as strength, weight, and thermal resistance. Some examples include:
- Glass-Filled Plastics: These materials offer increased rigidity and strength, making them ideal for load-bearing applications.
- Bio-Based Plastics: As sustainability becomes more crucial, bio-based plastics are increasingly utilized for their environmental advantages.
- Thermoplastic Elastomers (TPEs): TPEs provide flexibility and durability, suitable for applications demanding high elasticity.
Choosing the right materials not only improves product performance but also aligns with manufacturers’ sustainability goals.
Quality Control in Injection Molding
Testing Methods for Injection Molded Parts
Quality control is critical in ensuring that injection molded parts meet stringent industry standards. Common testing methods include:
- Dimensional Inspections: Using calipers and other measuring tools ensures that parts meet specified dimensions.
- Visual Inspections: Technicians perform visual assessments to detect flow marks, color inconsistencies, or surface defects.
- Mechanical Testing: Tests such as tensile strength measurement assess the durability and performance of the molded parts under stress.
These testing methods help ensure that only high-quality parts reach the market, which is essential for maintaining brand reputation and customer satisfaction.
Addressing Common Defects in Production
Defects in injection molded parts can lead to significant losses if not efficiently addressed. Common defects include:
- Short Shots: This occurs when there isn’t enough material filling the mold. Adjusting injection speed or increasing material temperature can resolve this issue.
- Flash: Flash appears as excess material at the parting line. This issue can be mitigated by ensuring the mold halves are properly aligned and clamped.
- Color Variation: Inconsistencies in color may arise from improper mixing of pigments. Ensuring uniform mixing and consistent material supply can alleviate this concern.
Regular monitoring of the molding process combined with these remedies can significantly reduce defects and enhance product quality.
Best Practices for Maintaining Quality Standards
Maintaining high quality in injection molded parts requires adherence to best practices, including:
- Standard Operating Procedures (SOPs): Develop comprehensive SOPs for the injection molding process to ensure consistency.
- Employee Training: Invest in training programs for employees to enhance their understanding of quality standards and operational techniques.
- Regular Equipment Maintenance: Ensure that all equipment is routinely serviced and calibrated to maintain precision in the molding process.
By embedding quality assurance into the manufacturing culture, companies can produce reliable, high-quality injection molded parts.
Future Trends in Injection Molding Technology
Advancements in Injection Molding Processes
The injection molding industry is continuously evolving, with advancements that promise to enhance efficiency and effectiveness. Some trends to watch include:
- Smart Injection Molding: Integrating IoT and smart sensors into injection molding machines allows for real-time monitoring and diagnostics, improving accuracy and reducing downtimes.
- Micro Molding: This technology enables the production of tiny, intricate components needed in electronics and medical devices with high precision.
- Multi-Material Injection Molding: This innovation allows for combining multiple materials in a single process, producing parts with varying properties in one cycle.
Keeping abreast of these trends allows manufacturers to capitalize on the latest technologies and improve production capabilities.
Impact of 3D Printing on Traditional Molding Methods
The rise of 3D printing has begun transforming traditional manufacturing methods, including injection molding. While injection molding remains the preferred method for mass production of parts due to its efficiency in large runs, 3D printing allows for:
- Rapid Prototyping: Designers can quickly create prototypes without the time and cost of traditional molds.
- Complex Geometries: 3D printing facilitates the production of parts with complexities that may not be possible with conventional molding.
- Customization: The method allows for individualized or small batch runs, appealing to niche markets.
Ultimately, the coexistence of these technologies could promote hybrid approaches, enhancing flexibility and market responsiveness.
Sustainability in the Production of Injection Molded Parts
Sustainability has emerged as a critical consideration within the injection molding industry. Efforts to reduce environmental impact include:
- Recyclable Materials: Utilizing thermoplastics that can be remelted and remolded cuts down on waste.
- Energy-Efficient Machines: The development of energy-efficient injection molding machines minimizes the carbon footprint of manufacturing operations.
- Waste Reduction Strategies: Implementing process improvements aimed at reducing scrap and optimizing material use enhances both economic and environmental outcomes.
By focusing on sustainable practices, injection molding manufacturers can contribute to a greener future while maintaining competitiveness in a changing market.