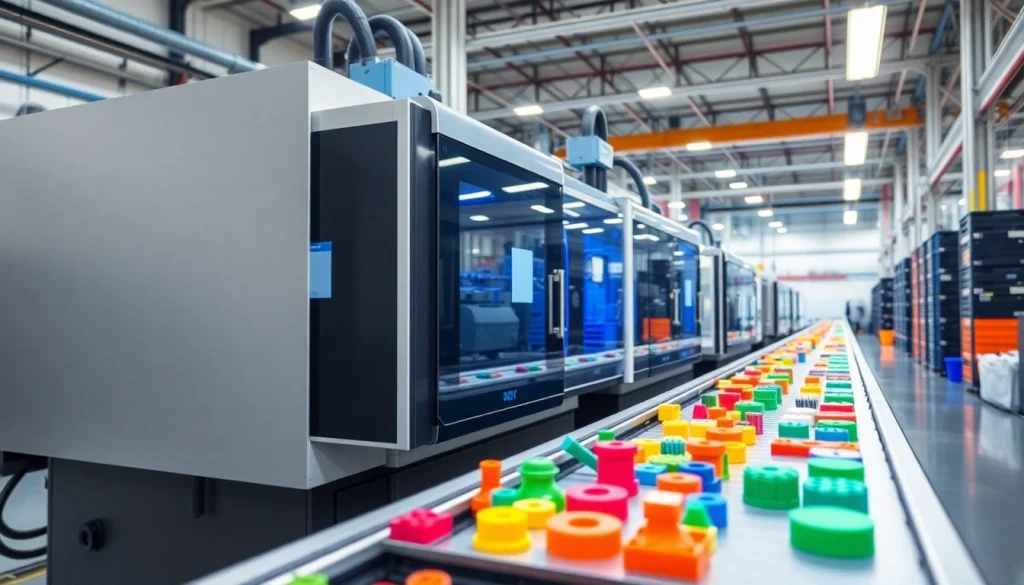
Understanding Injection Molded Parts
Injection molding has revolutionized the manufacturing industry, serving as a foundational process for producing a myriad of products we encounter daily. The efficiency and adaptability of this technique allow for high-volume production of intricate designs with remarkable precision, resulting in high-quality injection molded parts. In this comprehensive examination, we will delve into the essentials of injection molded parts, their applications, benefits, and how they are configured within the broader landscape of manufacturing processes.
The Basics of Injection Molding
Injection molding is a manufacturing process used to produce complex and detailed parts in large quantities. The process itself involves injecting molten material, typically plastic, into a mold which is then cooled to create the final part. Key steps include:
- Material Preparation: Raw material pellets, usually thermoplastics or thermosets, are fed into a hopper.
- Heating: The material is heated until it becomes molten in a barrel equipped with a reciprocating screw.
- Injection: The molten plastic is injected at high pressure into a mold.
- Cooling: The material cools and solidifies to form the part.
- Ejection: The finished part is ejected from the mold.
This method allows for high efficiency in producing a consistent quality of parts, which can be used across various applications, from consumer goods to industrial components.
Common Applications of Injection Molded Parts
Injection molded parts are found in numerous industries due to their versatility. Common applications include:
- Consumer Products: Items like bottles, caps, and kitchen utensils.
- Automotive Industry: Dashboards, paneling, and many other components.
- Electronics: Housings for phones, laptops, and other devices.
- Medical Devices: Components such as syringes and connectors.
- Industrial Equipment: Parts like gears, clamps, and various fixtures.
The endless possibilities for shapes and sizes make injection molding suitable for almost any product requirement.
The Benefits of Using Injection Molding
Injection molding comes with a multitude of advantages:
- High Efficiency: Capable of producing large quantities of precise parts in a short timeframe.
- Cost-Effectiveness: Reduces waste and efficient material usage, especially in large production runs.
- Complex Designs: Enables the creation of intricate shapes that would be difficult with other methods.
- Material Variety: A range of thermoplastics and thermosets can be used, offering various properties to suit specific needs.
- Consistency: High repeatability guarantees that parts are uniform across production batches.
Components of Injection Molding Machines
Understanding the machinery involved in injection molding is crucial to grasping how parts are produced. Each component plays a significant role in the overall functionality.
Essential Parts of Injection Molding Machines
The primary components of an injection molding machine include:
- Hopper: Holds the raw plastic granules before they enter the heating chamber.
- Barrel: Where the material is heated and melted for injection.
- Injection Unit: Executes the injection of molten material into the mold.
- Mold: The tool used to form the part once the molten material is injected.
- Clamping Unit: Holds the mold halves together during the injection process.
Functionality of Each Component
Each part of the injection molding machine is vital for efficient operation:
- Hopper: Allows for continuous feeding of the plastic pellets into the heating chamber.
- Barrel Configuration: Requires precision heating to ensure the material melts evenly without degrading.
- Injection Unit Mechanics: The unit must apply sufficient force to inject the molten material into the mold at the correct speed and timing.
- Mold Design: Needs to be engineered for easy ejection of parts and to withstand the pressures involved during molding.
- Clamping Unit Strength: Must maintain tight pressure during injection to prevent leakage or deformation of the molded part.
Maintenance of Injection Molding Equipment
Regular maintenance of injection molding machines is essential to ensure optimal performance:
- Routine Inspection: Checking for wear and damage to components.
- Cleaning: Regularly clear the barrel and hopper to avoid contamination.
- Lubrication: Keeping moving parts well-lubricated to ensure smooth operation.
- Calibration: Ensuring the machine settings are tailored for specific materials and products.
- Replacement Parts: Timely replacement of worn-out parts helps avoid production downtime.
Designing Effective Injection Molded Parts
The design of injection molded parts is crucial for their functionality and manufacturability. A well-designed part can significantly enhance the production process.
Key Design Considerations for Injection Molding
When designing parts for injection molding, several key factors must be considered:
- Draft Angles: Proper angles facilitate easy demolding of parts without damage.
- Wall Thickness: Uniform thickness prevents warping and ensures consistent cooling.
- Radii and Fillets: Sharp corners can hinder flow and create stress concentrations; gentle curves are preferred.
- Material Selection: Choosing materials that meet thermal, mechanical, and aesthetic requirements is essential.
Best Practices for Optimizing Part Design
To maximize the efficiency and effectiveness of injection molded parts, adhere to the following best practices:
- Design for Manufacturing (DFM): Collaborate with manufacturing engineers during the design phase.
- Minimize Part Count: Designing multifunctional parts can reduce assembly time and costs.
- Iterative Prototyping: Utilize prototypes to test functionality and manufacturability early in the design process.
- Implementation of Simulation Tools: Use CAD and CAE software to predict potential issues before physical production.
Common Design Mistakes to Avoid
Avoid these common pitfalls to enhance the design of injection molded parts:
- Ignoring Tolerances: Tight tolerances may not be feasible for injection molding without additional processes.
- Inadequate Venting: Poor design may trap air in the mold, leading to defects.
- Complex Internal Features: Designing complex geometries can complicate mold design and lead to production issues.
- Neglecting Post-Molding Processes: Consider how parts will be finished or assembled after molding.
Injection Molding Process Explained
The injection molding process, while seemingly straightforward, involves complexities that demand precision and control.
Step-by-Step Overview of the Injection Molding Process
The process proceeds as follows:
- Mold Preparation: The mold is secured in place within the clamping unit.
- Heating and Melting: Pellets are heated to their melting point to achieve a fluid state.
- Injection: Molten plastic is injected into the mold cavity.
- Cooling: The material cools and solidifies within the mold.
- Ejecting: The part is ejected from the mold, ready for inspection and further processing.
Factors Affecting the Injection Molding Process
Several elements can influence the efficiency and quality of the injection molding process:
- Material Properties: Different plastics behave uniquely under heat and pressure.
- Mold Temperature: Must be closely monitored; too hot or too cold can lead to defects.
- Injection Speed: Affects the flow of material and the final quality of the part.
- Pressure Settings: Insufficient pressure can result in short shots, while excess can cause flash.
Quality Control in Injection Molding
Quality control measures are essential for ensuring that each batch of parts meets specifications.
Steps may include:
- Visual Inspection: Checking for obvious defects in every batch of produced parts.
- Dimensional Checks: Verifying that parts adhere to the designed tolerances.
- Material Testing: Assessing the properties of materials used in production.
- Sampling and Statistical Process Control: Using statistical methods to ensure consistency across production.
Future Trends in Injection Molded Parts
The world of injection molding is continuously evolving, with several trends shaping the future of this manufacturing process.
Emerging Technologies in Injection Molding
A variety of emerging technologies are being integrated into the injection molding process:
- 3D Printing: Used for rapid prototyping, enabling faster design iterations.
- Smart Molding Processes: Automation and AI are being deployed to monitor and optimize production conditions in real time.
- Bioplastics: Eco-friendly materials are gaining popularity as manufacturers look to greener solutions.
- Additive Manufacturing: Complementary practices that enhance traditional molding methods.
Sustainability Practices in Injection Molding
As sustainability becomes more significant, the injection molding sector is focusing on reducing its environmental footprint:
- Recycling: Utilizing recycled materials where feasible to minimize waste.
- Energy Efficiency: Implementing energy-efficient machinery and practices.
- Waste Management: Developing strategies to minimize scrap and promote reprocessing of materials.
The Impact of Industry 4.0 on Injection Molded Parts
Industry 4.0 integrates IoT technology into the manufacturing process, significantly affecting how injection molded parts are produced:
- Real-Time Monitoring: Providing data-driven insights for better decision-making and optimization.
- Predictive Maintenance: Allowing for proactive repairs and reducing machine downtime.
- Enhanced Collaboration: Facilitating real-time communication between design, production, and supply chain management.