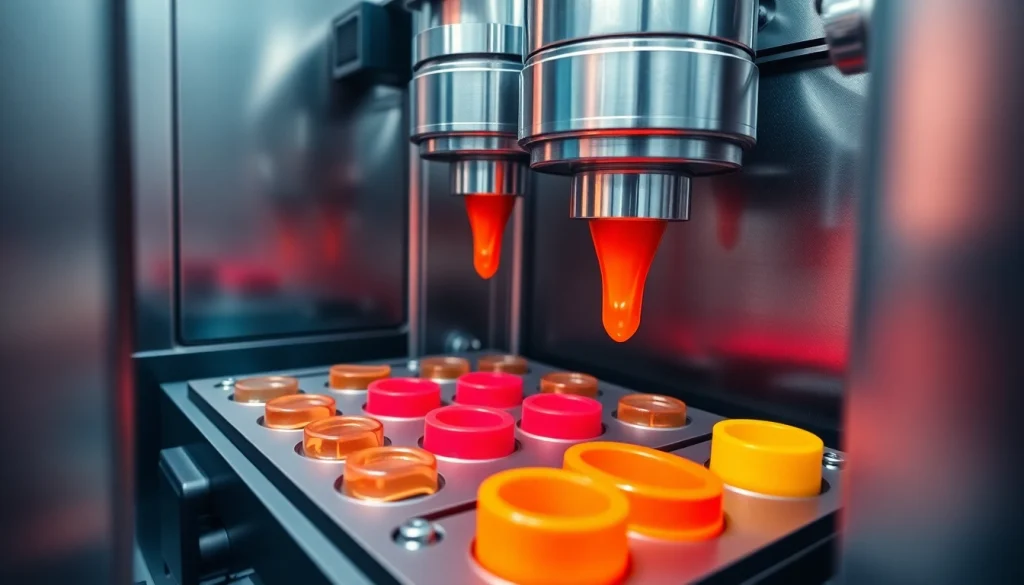
Understanding Injection Molded Parts
Injection molded parts are fundamental components in modern manufacturing and are pivotal to various industries. They are created through a precise process that allows for high-volume production of parts, ranging from prototypes to end-use components. Understanding the intricacies of injection molded parts can greatly enhance production efficiency, design quality, and product performance.
What Are Injection Molded Parts?
Injection molded parts are created by injecting molten material into a mold. Once the material cools and solidifies, it takes the shape of the mold, resulting in a finished product. This manufacturing method is notably efficient and is utilized for producing parts across various sectors, such as automotive, consumer goods, electronics, and medical devices.
The use of injection molds allows manufacturers to create complex geometries with high precision while maintaining tight tolerances. Common materials used include thermoplastics, thermosetting polymers, and metals, each chosen based on the requirements of the final product.
Key Stages of the Injection Molding Process
The injection molding process involves several critical stages that ensure quality and efficiency:
- Material Selection: Choosing the right material based on mechanical properties, cost, and application requirements.
- Mold Design: Creating a mold that accommodates the desired part shape and includes features such as ejector pins and cooling channels.
- Injection: Injecting molten plastic into the mold under high pressure, ensuring the material fills the entire cavity.
- Cooling: Allowing the material to cool and solidify before the mold is opened.
- Ejection: Removing the finished part from the mold using ejector pins or plates.
- Finishing: Performing post-processing such as trimming, machining, or adding surface treatments to enhance the final appearance and functionality.
Common Materials Used in Injection Molded Parts
Various materials are used in the injection molding process, each offering unique benefits:
- Thermoplastics: Such as polypropylene (PP), polyethylene (PE), and polystyrene (PS) are widely used due to their versatility and recyclability.
- Engineering Plastics: Including polycarbonate (PC) and nylon (PA), known for their superior mechanical properties and thermal resistance.
- Thermosets: Like epoxy and melamine, which provide high durability and heat resistance but cannot be remolded.
- Metal Alloys: In specialized applications where strength and rigidity are crucial.
Designing Effective Injection Molded Parts
The design phase is critical for the successful production of injection molded parts. Effective designs can minimize costs, optimize performance, and enhance functionality.
Best Practices for Part Design
When designing moldable parts, several best practices should be followed:
- Simplify Geometry: Avoid excessive complexity to reduce tooling costs and improve moldability.
- Uniform Wall Thickness: Ensure consistent wall thickness to prevent warping and ensure even cooling.
- Include Draft Angles: Adding draft angles facilitates easier ejection of the finished part from the mold.
- Utilize Ribs and Bosses: To enhance strength without increasing material usage.
Common Design Challenges and Solutions
Common challenges in designing injection molded parts include:
- Warpage: To combat this, achieve uniform wall thickness and control cooling rates to minimize internal stresses.
- Surface Finish: Quality can be affected by mold design flaws. Using proper mold textures can enhance the final appearance.
- Brittleness: Choosing the right materials and analyzing stress concentrations will improve durability.
Incorporating Tolerances and Specifications
Establishing precise tolerances is vital in injection molding. Specifications should consider:
- Dimensional Accuracy: Ensuring parts meet design specifications through accurate mold manufacturing.
- Functional Tolerances: These are critical for components that require precise fits, such as hinges or assembly parts.
- Aesthetic Considerations: Addressing the finish and color to ensure product attractiveness and marketability.
Applications of Injection Molded Parts
Injection molded parts are a cornerstone of many industries due to their flexibility and efficiency, allowing for the production of a diverse range of products.
Industries Utilizing Injection Molded Parts
Some industries that prominently use injection molding include:
- Automotive: For producing durable parts like dashboards, panels, and components.
- Consumer Goods: Including household items such as toys, kitchenware, and tools.
- Healthcare: Creating medical devices, syringes, and other precision instruments.
- Electronics: Producing casings, connectors, and other electronic components.
Everyday Products Made from Injection Molding
Many common products are made using injection molding, including:
- Plastic containers and bottles
- Household appliances
- Automotive parts like bumpers and instrument panels
- Personal care products, such as tubes and caps
Case Study: Successful Applications
One notable case of successful injection molding application is in the automotive industry, where manufacturers have improved production efficiency by using advanced injection molding techniques. For example, a leading automotive supplier reduced production time by 20% and material waste by 15% by implementing optimized mold designs and more effective material selection.
Optimizing Production for Injection Molded Parts
To maximize the efficiency and quality of injection molded parts, production optimization is paramount. This entails a combination of machine settings, monitoring, and quality control.
Machine Setup and Configuration
The efficiency of the injection molding process largely depends on the proper setup of the injection molding machine. Key considerations include:
- Temperature Control: Ensuring that the barrel and mold temperatures are set according to the material used to avoid defects.
- Injection Speed: Adjusting the speed to balance between filling the mold effectively without causing defects like flash.
- Pressure Settings: Optimizing injection pressure to achieve a good fill while minimizing stress.
Quality Control in Injection Molding
Quality control measures must be implemented throughout production. This includes:
- Regular Inspections: Perform in-process inspections to catch any defects early in the process.
- Feedback Loops: Use data from finished products to continually refine processes and molds.
- Testing and Validation: Employ different testing methods (like stress tests) to ensure parts meet functional standards.
Cost-Effective Strategies for Production
Cost-effectiveness in production can be achieved through several strategies:
- Material Optimization: Select materials that balance cost and performance.
- Lean Manufacturing Principles: Implement practices that minimize waste, such as just-in-time production.
- Automation: Invest in automated systems that increase throughput and reduce manual labor costs.
Future Trends in Injection Molded Parts Manufacturing
As technology continues to evolve, the injection molding industry is witnessing transformative trends that enhance efficiency and sustainability.
Advancements in Technology and Materials
Recent advancements in technology include the use of advanced robotics in the molding process, which increases precision and speed. New materials, such as bio-based plastics, are being developed to offer better properties and environmental friendliness, which can lead to more sustainable production processes.
Sustainability Practices in Injection Molding
Sustainability is becoming a cornerstone of manufacturing practices. Companies are investing in recycling programs, using eco-friendly materials, and designing products for disassembly to ensure they can be recycled at the end of their lifespans. These practices not only minimize environmental impact but can also lead to cost reductions in material sourcing.
The Future of Custom Injection Molded Parts
The need for customization in injection molded parts is on the rise. Advances in software and mold-making techniques allow for rapid prototyping and small batch production, enabling manufacturers to respond quickly to market demands. We can expect to see greater customization options that not only fulfill functional requirements but also resonate with consumer preferences for personalized products.