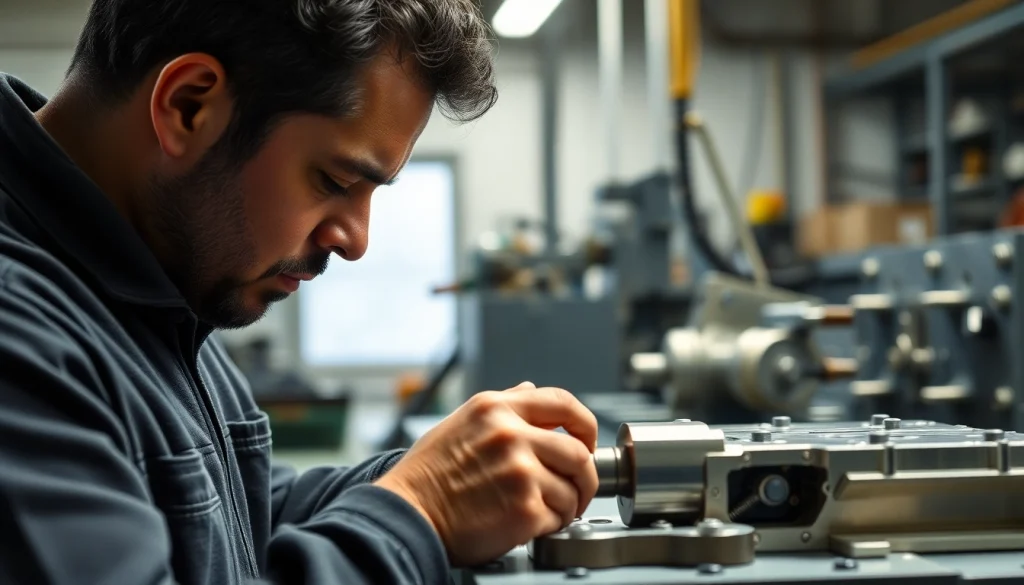
Understanding the Role of a Mold Maker for Injection Molding
The role of a mold maker for injection molding is crucial in the manufacturing of plastic products. Mold makers are skilled professionals who design, create, and maintain molds that are used in the injection molding process. A thorough understanding of their capabilities and contributions is essential for businesses looking to optimize production processes and improve product quality.
What Does a Mold Maker Do?
A mold maker is responsible for a variety of tasks, which can be categorized into design, fabrication, assembly, and maintenance of molds. They work closely with design engineers to translate concepts into functional molds, ensuring that the final product meets specifications. Additionally, mold makers utilize various methods and machinery, including CNC (Computer Numerical Control) machines, to precisely shape mold components from materials like steel or aluminum. Once the mold is fabricated, mold makers conduct trials to verify that the mold functions correctly and can produce parts that conform to quality standards.
Key Skills and Qualifications of Mold Makers
To excel in this field, mold makers must possess a blend of technical skills and mechanical aptitude. Key qualifications include:
- Technical Training: Many mold makers undergo formal training through technical schools or apprenticeships in machining and mold design.
- Mathematical Proficiency: A strong understanding of geometry and trigonometry is essential for creating precise designs.
- CNC Machining Skills: Familiarity with CNC programming and operation is critical, as many modern molds are produced using CNC machines.
- Problem-Solving Abilities: Mold makers must troubleshoot issues that may arise during the mold-making process or while testing molds.
Importance of Precision in Mold Making
The precision of a mold directly impacts the quality of the final product. Even minor errors in mold design or fabrication can lead to defects such as warping, incomplete filling, or poor surface finishes in molded parts. Therefore, meticulous attention to detail is a hallmark of effective mold making. The use of advanced technologies, such as 3D modeling software and precise machining tools, significantly enhances the accuracy of mold production, resulting in higher-quality end products.
Types of Injection Molds
In the field of injection molding, several types of molds are commonly used, each serving different purposes based on product requirements, production volume, and material specifications.
Single-Cavity vs. Multi-Cavity Molds
Single-cavity molds are designed to produce one part at a time. They are often used for low-volume production runs or for making prototypes. In contrast, multi-cavity molds can create multiple parts in a single cycle, making them more suitable for high-volume production. Choosing between single and multi-cavity molds depends on factors such as budget, time constraints, and the intended use of the product.
Hot Runner vs. Cold Runner Systems
Mold systems can also vary based on runner design. Hot runner systems maintain the plastic material in a molten state, allowing for faster cycle times and less waste, as there is no solidified material to remove after each cycle. Cold runner systems, on the other hand, require additional time for the material to cool and may generate more waste due to sprue and runner materials that are discarded. The choice between the two systems depends on production costs, the complexity of the mold, and the desired properties of the final product.
Choosing the Right Mold Type for Your Project
When selecting a mold type, consider factors such as:
- Production Volume: Higher volumes often justify the investment in multi-cavity or hot runner molds.
- Material Characteristics: Different materials may perform better with specific mold types.
- Project Timeline: Consider the lead time for mold fabrication as it can impact project schedules.
Factors Influencing the Cost of Mold Making
The cost of making molds can vary widely, influenced by several critical factors. Understanding these variables can help businesses make more informed financial decisions.
Material Selection and Its Impact
The choice of materials for molds directly affects both cost and quality. High-quality steel molds, while more expensive, tend to offer greater durability and longevity compared to aluminum molds, which may be less expensive upfront but wear out faster. Additionally, the type of plastic being molded and the expected production volume should correlate with the material selection to optimize cost efficiency.
Complexity of the Mold Design
A more complex mold design, which may include intricate geometries and features, will generally incur higher costs due to the increased time and technical expertise required to produce it. Moreover, complex designs often necessitate advanced machining techniques that can further contribute to higher expenses. Hence, simplifying designs where possible can lead to cost savings.
Finding Cost-Effective Solutions
To control costs in mold making, businesses can consider various strategies:
- Design for Manufacturability: Simplifying designs to enhance manufacturability can significantly reduce costs.
- Collaborating with Mold Makers: Engaging early with mold makers can help identify potential cost-saving opportunities in design and material selection.
- Utilizing Standard Components: Whenever feasible, using standard, off-the-shelf components instead of custom parts can lower production costs.
Finding the Right Mold Maker for Injection Molding
Selecting the right mold maker is essential for ensuring the success of an injection molding project. Proper vetting of potential partners can result in better quality and performance of the molds produced.
Evaluating Experience and Expertise
One of the first steps in finding a mold maker is assessing their experience and expertise. Key factors to consider include:
- Industry Experience: Look for mold makers with experience in your specific industry or application.
- Portfolio of Previous Work: Evaluate their previous projects and client testimonials to assess their capabilities.
- Technological Capabilities: Ensure they have the latest technology and equipment necessary for precision mold making.
Assessing Customer Reviews and Testimonials
Reviews from previous clients can provide valuable insights into a mold maker’s reliability, quality of work, and customer service. Look for both qualitative feedback and quantitative ratings to understand how well the mold maker performs under various circumstances.
Requesting Quotes and Budgeting
Once you have a shortlist of potential mold makers, request detailed quotes. Be sure to provide them with comprehensive information about your project, including design specifications, desired materials, and estimated production volumes. Comparing quotes not just for pricing, but for the value offered can aid in making the most economical choice.
Future Trends in Mold Making and Injection Molding
The industry of mold making and injection molding is evolving rapidly, driven by advancements in technology and changing market demands. Staying abreast of these changes is essential for businesses looking to remain competitive.
Advancements in Technology and Materials
Recent advancements in automation, artificial intelligence, and CAD software are revolutionizing the mold-making process. High-speed machining and additive manufacturing are becoming integral, allowing for quicker prototype development and reduced turnaround times. Moreover, the development of new materials such as lightweight composites and advanced thermoplastics is enhancing mold performance and durability.
Sustainable Practices in Mold Production
As businesses strive for sustainability, mold makers are increasingly adopting eco-friendly practices. This includes using recycled materials, reducing waste through optimized processes, and implementing energy-efficient technologies. These practices not only minimize environmental impact but can also lead to significant cost savings.
The Impact of 3D Printing on Mold Making
3D printing is emerging as a game-changer in mold making. This technology allows for rapid prototyping of molds, which accelerates the design process. Additionally, 3D printing enables the production of complex mold geometries that were previously challenging or impossible to create with traditional methods. As the capabilities of 3D printing expand, we can expect significant shifts in how molds are designed and manufactured.