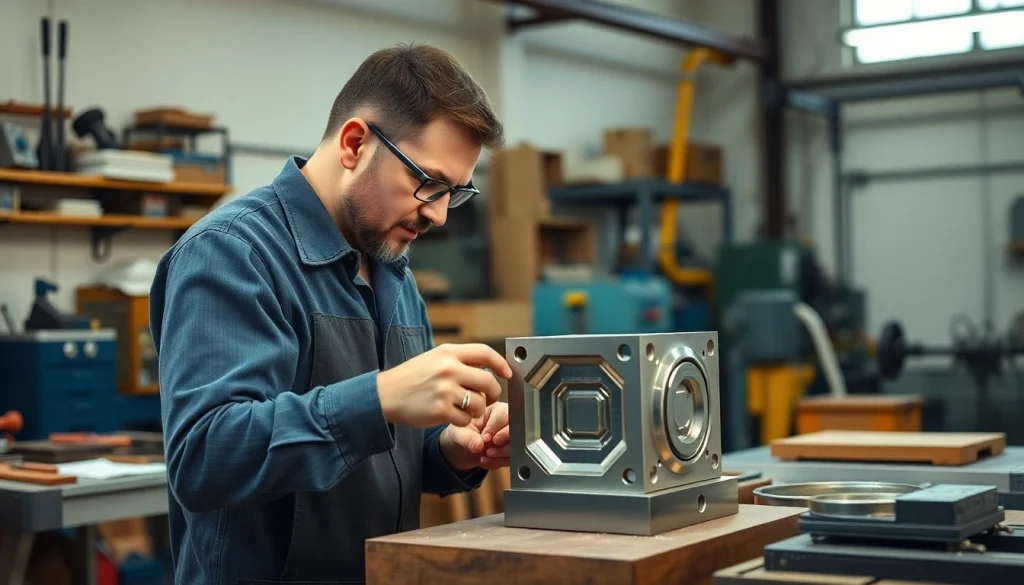
Understanding the Role of a Mold Maker for Injection Molding
As industries evolve, the demand for high-quality, precise molding processes has escalated significantly. One vital component of this process is the role of the mold maker for injection molding, who is responsible for designing, creating, and refining the molds used to produce plastic parts. Their expertise not only influences the cost and quality of the final products but also impacts manufacturing efficiency and turnaround times. In this article, we will delve into the specifics of what a mold maker does, the importance of their expertise, and the various types of molds used in the injection molding process.
What Does a Mold Maker Do?
A mold maker engages in the intricate process of creating molds for plastic injection molding. This involves:
- Designing Molds: Mold makers use CAD (Computer-Aided Design) software to design intricate molds based on specifications provided by clients. This process involves critical thinking and creativity to ensure that the mold design facilitates efficient production.
- Building Molds: Following the design phase, mold makers fabricate the molds using various materials such as steel, aluminum, or polymers. This process may involve machining, casting, or additive manufacturing techniques to achieve precision.
- Testing and Refining: Once the molds are built, they undergo testing to identify any defects or areas for improvement. Mold makers must be adept at interpreting the production results and making necessary adjustments.
- Maintenance and Repairs: A key aspect of a mold maker’s job is to ensure that the molds are well-maintained to prolong their lifespan and efficiency. Regular maintenance can prevent costly downtimes due to mold failure.
Importance of Expertise in Mold Making
The expertise of a mold maker is paramount in achieving the best results in injection molding. Some of the critical reasons for prioritizing skilled mold makers include:
- Quality Control: Skilled mold makers ensure that the finished molds yield products of consistent quality, thereby minimizing waste and rework.
- Cost Efficiency: Experience in mold making allows for more efficient designs and the ability to select the right materials, significantly lowering production costs over time.
- Problem Solving: A seasoned mold maker can anticipate potential issues and develop solutions even before they arise, ensuring smoother production processes.
- Innovation: Expertise often leads to innovative solutions and techniques that can enhance production efficiency and product quality.
Types of Molds Used in Injection Molding
Understanding the various types of molds is crucial for businesses looking to optimize their injection molding processes:
- Single-Cavity Molds: Ideal for low-volume production, these molds contain a single cavity. They are cost-effective for simpler projects.
- Multiple-Cavity Molds: Designed to produce several parts in one cycle, these molds enhance production efficiency, making them suitable for medium to high-volume production.
- Family Molds: These molds contain multiple cavities to produce different parts in a single cycle. They are beneficial for producing parts that are used together.
- Stack Molds: Stack molds consist of multiple mold layers, allowing for multiple parts to be produced simultaneously. They help maximize productivity and reduce cycle times.
- Hot Runner Molds: These molds minimize waste by keeping the plastic in a molten state in the runners, thus reducing cycle times and material usage.
Key Factors in Selecting a Mold Maker
Choosing the right mold maker is crucial for the success of any injection molding project. Here are some factors to consider:
Evaluating Experience and Skills
When selecting a mold maker, assess their experience and realm of expertise. Key considerations include:
- Industry Experience: Look for a mold maker who has a proven track record in your specific industry, as they will be better equipped to understand the unique requirements and challenges.
- Technical Skills: Analyze their knowledge of CAD/CAM software, machining techniques, and material selection.
- References and Case Studies: Request references and review past projects to evaluate their capabilities and success rates.
Assessing Facility Capabilities and Technology
The capabilities of the mold maker’s facility directly impact the quality and efficiency of the mold production process:
- Machinery: Ensure that the mold maker has access to advanced machinery and technologies necessary for high-precision mold production.
- Material Handling: Check if they have the capacity to handle diverse materials suited for your project requirements.
- Scalability: Consider if the mold maker can scale production up or down in response to your project’s demands.
Understanding Material Selection
Material selection is a critical factor influencing mold longevity and product quality:
- Durability: Choose a mold maker who understands the importance of selecting durable materials that can withstand high pressure and temperature during the injection molding process.
- Cost-Effectiveness: Assess the balance between cost and quality, ensuring that the materials chosen align with your budget and specifications.
- Compatibility: Ensure that the materials used for molds are suitable for the specific type of plastics that you intend to mold.
Cost Considerations for Injection Mold Making
Cost is always a significant factor when considering injection mold making, and it varies based on several key considerations:
Breakdown of Mold Manufacturing Costs
The overall costs associated with mold making can include the following elements:
- Design Costs: These include the expenses associated with mold design services and CAD software utilization.
- Material Costs: Depending on the type of mold being produced, the selection of materials can significantly impact the total cost.
- Labor Costs: Consider the costs associated with skilled labor for both building and testing the molds.
- Maintenance Costs: Regular maintenance is essential to prolong mold life and keep production efficient, contributing to long-term costs.
How Complexity Affects Price
The complexity of the mold design and functionality heavily influences the price:
- Simple Molds: Generally range from $3,000 to $6,000, suitable for straightforward designs.
- Complex Molds: Multi-cavity or intricate designs can reach upwards of $25,000 to $50,000 or more, particularly if they require advanced technologies or materials.
- Long-Run vs. Short-Run Molds: Long-run molds are more expensive initially, but they yield a lower cost per part over time compared to short-run molds.
Long-Term Investment vs. Short-Term Savings
While opting for cheaper mold making options might seem appealing, long-term considerations should guide your decision:
- Mold Longevity: Investing in high-quality molds may decrease the frequency of replacements and repairs.
- Quality Assurance: Higher-quality molds often produce superior parts, reducing defects and waste, ultimately saving costs in the production cycle.
- Maintenance Savings: Well-made molds require less maintenance, translating into lower operational costs over time.
Best Practices for Working with Your Mold Maker
Effective collaboration with your mold maker can drastically enhance the outcome of your project. Here are best practices to implement:
Establishing Clear Communication
Open and clear communication channels between you and your mold maker should be established from the outset.
- Set Expectations: Clearly outline your expectations regarding timelines, quality, and costs at the initial meeting.
- Frequent Updates: Request regular updates during the mold-making process to monitor progress and address any concerns promptly.
- Feedback Loop: Encourage a feedback loop where both parties can discuss challenges faced during the process and suggest improvements.
Providing Detailed Specifications
A comprehensive set of specifications is crucial for ensuring that the mold maker can accurately produce what you need:
- Design Characteristics: Include detailed dimensions, tolerances, and material specifications to minimize assumptions and errors.
- Performance Requirements: Specify how the produced parts are expected to perform, along with any regulatory or industry standards they must meet.
- Prototypes: If possible, provide prototypes or mock-ups to give a visual reference for which the mold will be based.
Conducting Regular Reviews and Adjustments
Regular reviews can help ensure that the project stays on track and meets your expectations:
- Scheduled Review Meetings: Establish a timeline for review meetings to assess mold development progress, allowing for timely adjustments.
- Testing Phases: Implement testing phases where molds can be evaluated for functionality before full-scale production begins.
- Adaptability: Stay flexible to changes in the project scope, as unforeseen challenges may necessitate adjustments to the initial plan.
Future Trends in Mold Making for Injection Molding
As we look ahead, several trends are shaping the future of mold making in injection molding:
Technological Advancements in Mold Design
Emerging technologies are continually transforming mold design and production:
- 3D Printing: This technology allows for rapid prototyping, enabling mold makers to test designs quickly and efficiently.
- Simulation Software: Advanced simulation tools are utilized to analyze molds before production, helping to predict potential issues and optimize designs.
- Cloud-Based Collaboration: Enhanced connectivity facilitates seamless collaboration between mold makers and manufacturers across the globe.
Sustainability in Materials and Processes
The growing emphasis on sustainability is affecting how molds are made:
- Recyclable Materials: Many mold makers are beginning to use recyclable materials that can reduce environmental impact.
- Energy Efficiency: Techniques and machinery that consume less energy are being prioritized, offering both financial and environmental savings.
- Life-Cycle Assessment: Assessing the environmental impact of the entire mold lifecycle encourages sustainable practices throughout the production process.
Impact of Automation on the Mold Making Industry
Automation is reshaping the mold-making landscape:
- Increased Efficiency: Automated processes can increase productivity and precision through reduced human error in mold fabrication.
- Cost Reduction: While the initial investment in automation may be high, long-term savings due to efficiency gains and minimized labor costs make it appealing.
- Skilled Workforce Adaptation: As automation becomes more prevalent, the demand for skilled workers who can operate and maintain these technologies will rise.