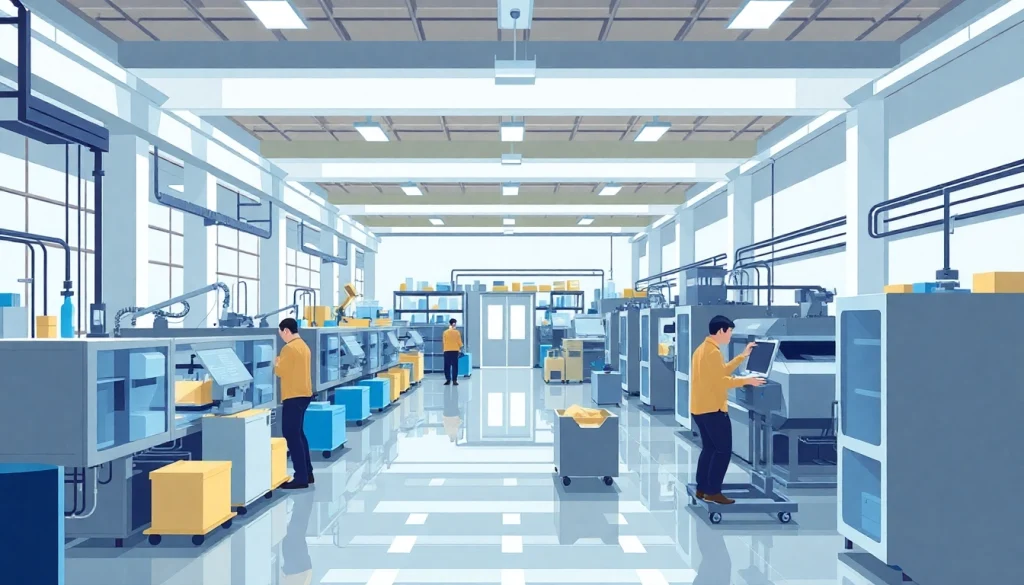
Introduction to Plastic Manufacturing
The manufacture of plastic parts is a pivotal component of modern manufacturing, serving a broad range of industries from automotive to consumer goods. As we advance in our technological capabilities, understanding the intricate processes and materials involved in plastic manufacturing becomes increasingly essential. This article aims to delve deeply into the various methods and techniques of plastic part production, emphasizing best practices, industry standards, and innovations driving the sector forward.
Understanding Different Types of Plastics
Plastics are categorized broadly into two primary types: thermoplastics and thermosetting plastics. Thermoplastics, such as polyethylene and polypropylene, can be remelted and reshaped multiple times, making them versatile for various manufacturing processes. In contrast, thermosetting plastics, like epoxy and phenolic, undergo a chemical change when heated that prevents them from being remelted. This distinction affects not only the choice of manufacturing process but also the end-use application of the plastic parts.
The Importance of the Manufacture of Plastic Parts
Plastic parts are ubiquitous in everyday life, from the packaging of food items to the components of complex machinery. Their lightweight nature, durability, and ability to be molded into intricate shapes contribute to their significance in manufacturing. The efficient manufacture of plastic parts enables cost-effective production and innovation in product design, hence driving critical industries forward.
Overview of Manufacturing Processes
Several manufacturing processes can be employed in the production of plastic parts, including injection molding, extrusion, blow molding, and compression molding. Each method has its unique advantages, suitability based on production volume, design complexity, and material properties. For more detailed insights, you may explore the manufacture of plastic parts through expert resources tailored to specific applications.
Key Techniques in the Manufacture of Plastic Parts
Injection Molding Process Explained
Injection molding is the most popular method for producing plastic parts. During this process, plastic pellets are heated until they turn into a molten state, which is then injected into a mold. Once cooled, the mold is opened, and the solidified part is ejected. This technique is renowned for its ability to produce high volumes of identical parts with precision. Factors determining the success of injection molding include mold design, temperature control, and material selection. It is particularly favored for producing complex designs and intricate geometries, making it invaluable in industries requiring detailed components like consumer electronics and automotive parts.
Alternative Methods: Extrusion and Blow Molding
Extrusion involves forcing molten plastic through a die to create continuous shapes, such as pipes or sheets. This method is often used for manufacturing large quantities of consistent profiles and is beneficial in applications like packaging or construction. Blow molding, on the other hand, is particularly applied to hollow plastic objects, such as bottles. Here, air is blown into a molded parison to expand it and fill the mold, creating the final hollow shape. Both methods have become essential in specific industries, enabling efficient production of bulk items.
Comparing Techniques: Efficiency and Costs
When evaluating manufacturing techniques, efficiency and costs are paramount considerations. Injection molding often has higher initial setup costs due to the expensive molds, yet it is the most cost-effective method for large-scale production owing to its speed and the minimal waste generated. Conversely, processes like extrusion may have lower startup costs, making them advantageous for shorter runs or less complex shapes. Understanding these dynamics allows manufacturers to optimize production based on project requirements.
Materials Used in Plastic Part Production
Choosing the Right Material for Your Project
Selecting the appropriate material is crucial for the performance of plastic parts. Common materials include ABS, polystyrene, nylon, and polyethylene, each with distinct properties. For instance, ABS is known for its toughness, making it suitable for consumer products, while nylon offers excellent abrasion resistance ideal for automotive parts. The choice depends on the mechanical requirements, aesthetic preferences, and environmental considerations associated with the final application.
Recyclability and Sustainability of Materials
As environmental concerns escalate, the recyclability of materials becomes a crucial factor in the design and manufacture of plastic parts. Many manufacturers are now using recyclable polymers, and advances in technology allow degraded plastic material to be reused without significant quality loss. This shift towards sustainability not only addresses ecological concerns but also improves the overall efficiency of production cycles in the plastics industry.
Innovative Materials in Modern Manufacturing
Innovation in material science is driving the evolution of plastic manufacturing. Bioplastics, derived from renewable resources, are gaining traction, particularly in packaging applications where biodegradability is an asset. Additionally, advanced composites incorporating fibers or additives to enhance physical properties are becoming mainstream, allowing for the creation of lighter, stronger parts that can withstand harsher environmental conditions. Staying abreast of these innovations is vital for manufacturers aiming to differentiate their offerings.
Quality Control in Plastic Manufacturing
Importance of Quality Assurance
Quality assurance (QA) is vital throughout the plastic manufacturing process, ensuring that products meet stringent specifications and customer expectations. Implementing a robust QA system helps identify defects early, reducing waste and production costs. Engaging in regular audits and assessments can enhance the quality of output, ensuring reliable performance in the finished products.
Testing Methods for Durability and Reliability
Durability and reliability testing of plastic parts can include tensile testing, impact resistance tests, and environmental testing. These tests simulate conditions the parts will face in real-world applications, providing valuable data on their performance. Establishing a standardized testing regimen is fundamental to achieving compliance with industry standards and regulations.
Common Challenges and Solutions
Manufacturers often face challenges such as material inconsistencies, equipment failures, and design limitations. Implementing predictive maintenance for machinery can mitigate downtime, while ensuring a reliable supply chain for materials promotes consistency. Engaging cross-functional teams to address design-related challenges early in the product development process fosters innovation and enhances problem-solving capabilities.
Future Trends in the Manufacture of Plastic Parts
Technological Innovations on the Horizon
The future of plastic manufacturing is closely tied to technological advancements such as automation, artificial intelligence, and 3D printing. These innovations enhance precision, speed, and efficiency, reducing lead times and overall manufacturing costs. Emerging technologies are also paving the way for on-demand production, allowing manufacturers to respond swiftly to market needs without the overhead of maintaining large inventories.
Impact of Regulations on the Plastic Industry
As regulations concerning environmental standards intensify globally, the plastic manufacturing industry faces the imperative of compliance. Government policies promoting recycling and sustainability will require companies to reevaluate their material choices and manufacturing processes. Staying informed and proactive about compliance will be essential for manufacturers aiming to thrive in this evolving regulatory landscape.
Emphasis on Sustainable Practices
The drive towards sustainability is reshaping plastic manufacturing. Industry leaders are investing in sustainable practices, from utilizing renewable energy sources in production to developing closed-loop systems that minimize waste. Employers are increasingly seeking certifications that demonstrate environmental responsibility, making sustainability not just a trend, but a business imperative that resonates deeply with consumers today.