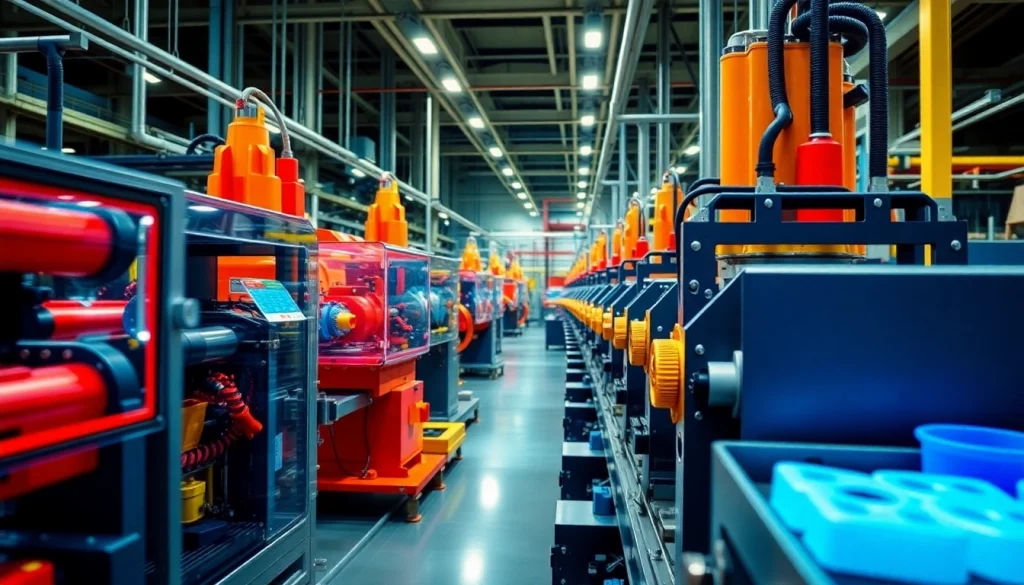
Understanding Blow Moulded Plastic Parts
In the realm of manufacturing, blow moulded plastic parts have gained significant traction due to their versatility and efficiency. This article delves into the intricacies of blow moulding, a robust process designed to create hollow plastic components for various applications. From understanding what blow moulded plastic parts are to exploring the diverse materials used in their production, we will cover essential aspects and trends shaping this industry.
What Are Blow Moulded Plastic Parts?
Blow moulded plastic parts are hollow structures manufactured using a process that involves inflating a heated parison (a tube of plastic) in a mould. This technique is highly efficient for producing various items ranging from bottles to complex automotive components. The end products are characterized by their lightweight, strength, and thermal stability, making them ideal for both consumer and industrial applications.
The Blow Moulding Process Explained
The blow moulding process follows several critical steps:
- Heating the Parison: The process begins with a plastic parison, which is heated to its melting point to ensure it can expand effectively.
- Mould Closing: Once heated, the parison is placed between the two halves of a mould, which quickly closes around it.
- Blowing Air: Compressed air is injected into the parison, inflating it like a balloon until it presses against the mould’s walls, thereby taking its shape.
- Cooling and Ejection: After the part has cooled and solidified, the mould opens, and the finished blow moulded part is ejected.
This well-orchestrated process is crucial in ensuring high-quality outputs while minimizing material waste.
Types of Blow Moulding Techniques
Blow moulding encompasses three primary techniques, each suited for specific applications:
- Extrusion Blow Moulding (EBM): This is the most common technique used for creating hollow plastic parts. A continuous tube of molten plastic is extruded and then formed into the desired shape.
- Injection Blow Moulding (IBM): In this technique, the process starts with the injection of molten plastic into a preform mould. The preform is then transferred to a blow mould where air is used to form the final shape.
- Injection Stretch Blow Moulding (ISBM): Similar to IBM, this method involves stretching the preform before blowing. This enhances the strength and clarity of the final product, making it an excellent choice for producing bottles.
Understanding these processes enables manufacturers to select the most effective method for producing blow moulded products based on specific performance requirements.
Materials Used in Blow Moulded Products
The choice of materials for blow moulded products plays a pivotal role in determining the functionality, durability, and aesthetic appeal of the final goods. Various types of plastics are utilized in the blow moulding process, offering a spectrum of properties and uses.
Common Plastics for Blow Moulding
Some of the most commonly used plastics in blow moulding include:
- Polyethylene (PE): Offers excellent barrier properties and flexibility, available in high-density (HDPE), low-density (LDPE), and linear low-density (LLDPE) variants.
- Polypropylene (PP): Known for its resistance to fatigue and impact, making it ideal for applications needing durability.
- Polyethylene Terephthalate (PET): Commonly used for beverage bottles due to its strength and recyclability.
- Polyvinyl Chloride (PVC): Offers excellent chemical resistance, which makes it suitable for specialized applications.
Choosing the Right Material for Your Product
Selecting the right material for blow moulded parts requires careful consideration of various factors:
- Functionality: Determine the physical requirements of the product, including strength, flexibility, and thermal resistance.
- Cost: Balance the material’s performance with budget constraints to ensure competitiveness in the market.
- Environmental Impact: Consider sustainability and the material’s recyclability to adhere to modern eco-friendly practices.
Advantages of Specific Plastics in Blow Moulding
Specific plastics offer unique benefits in their performance as materials for blow moulding:
- PE: Known for its low cost and high availability, PE is also versatile and can be adapted to various applications.
- PP: It offers superior resistance to high temperatures and can maintain its rigidity, making it suitable for long-term products.
- PET: Its excellent barrier properties make it a favorite for food and beverage containers, contributing to prolonged shelf life.
Applications of Blow Moulded Plastic Parts
The applicability of blow moulded plastic parts is extensive, spanning multiple industries and unique product categories.
Industry Applications: From Bottles to Automotive
Blow moulding is utilized across various industries, reflecting its versatility:
- Beverage Industry: Beverage bottles, including water, soda, and juices, heavily rely on blow moulding due to PET’s properties.
- Automotive: Blow moulded components are used in vehicle interiors, exterior parts, and under-the-hood applications.
- Personal Care: Bottles for shampoos, conditioners, and lotions, benefiting from the aesthetic and functional properties of blow moulded designs.
Consumer Products Made from Blow Moulded Plastics
Beyond industrial applications, many everyday consumer products are crafted through blow moulding:
- Toys: Many plastic toys utilize blow moulding for lightweight, hollow designs that are easy to handle.
- Containers: Storage containers, bins, and other household items are efficiently produced through blow moulding.
- Decorative Items: Hollow vases and ornamental pieces demonstrate the aesthetic capabilities of blow moulded plastics.
Customization and Design Flexibility
Blow moulding enables significant customization, allowing manufacturers to create products tailored to specific customer needs:
- Shapes and Sizes: Moulds can be designed to produce an almost infinite variety of shapes and sizes.
- Texturing and Finishes: Surface textures can be integrated into the mould design, enhancing the product’s aesthetic appeal.
- Multi-Layer Designs: Advanced techniques allow producers to create multilayer structures that enhance product advantages.
Quality Assurance in Manufacturing Blow Moulded Parts
Maintaining quality in blow moulding is essential for ensuring the performance and reliability of the products. Companies implement rigorous quality assurance processes to uphold standards.
Key Standards and Certifications
Manufacturers often adhere to various standards and certifications to guarantee product quality:
- ISO Certification: International Organization for Standardization certifications provide a framework for quality management.
- ASTM Standards: The American Society for Testing and Materials standards guide testing methods specific to plastics, ensuring compliance and safety.
Testing Procedures for Quality Control
To maintain high standards, testing procedures include:
- Material Testing: Assessing the properties of materials before and after processing.
- Dimensional Checks: Ensuring that the final products meet specified tolerances and design criteria.
- Functional Testing: Performing real-world tests to validate product performance under expected use conditions.
Continuous Improvement Practices
Adopting a culture of continuous improvement enables companies to enhance their processes and products:
- Feedback Loops: Utilizing customer feedback to refine designs and production methods.
- Employee Training: Investing in workforce education on latest techniques and technologies.
- Lean Manufacturing: Implementing lean practices to reduce waste and increase operational efficiencies.
Future Trends in Blow Moulded Plastic Manufacturing
The blow moulding industry is continuously evolving, influenced by advancements in technology, sustainability, and market demands.
Innovations in Blow Moulding Technology
Recent innovations are shaping the future of blow moulding:
- Automated Production Lines: Increased automation enhances efficiency, accuracy, and reduces production costs.
- 3D Printing: The intersection of 3D printing and blow moulding opens up opportunities for rapid prototyping and custom mould creation.
- Advanced Simulation Software: Software tools now allow manufacturers to simulate the blow moulding process, optimizing design before physical production.
Environmental Considerations and Sustainability
As consumer demand for sustainability rises, the industry is adapting:
- Recycled Plastics: Using recycled materials for blow moulding not only reduces waste but also meets growing environmental standards.
- Biodegradable Plastics: Research into biodegradable materials suitable for blow moulding is paving the way for greener alternatives in various applications.
- Energy Efficiency: Manufacturers are investing in energy-efficient machinery to lower their carbon footprint during production.
The Impact of Automation in Production
Automation is revolutionizing blow moulding operations by:
- Improving Precision: Automated systems offer enhanced precision in production, leading to fewer defects and waste.
- Reducing Labor Costs: With more processes automated, labor costs can be significantly reduced, enhancing profitability.
- Enhancing Safety: Automation minimizes the risk of workplace injuries by reducing the need for manual handling of heavy materials.
In conclusion, blow moulded plastic parts represent a critical component of modern manufacturing, spanning a wide array of industries and applications. Understanding the complexities of the blow moulding process, material selection, quality assurance, and future trends is essential for businesses aiming to leverage this versatile manufacturing technique effectively.