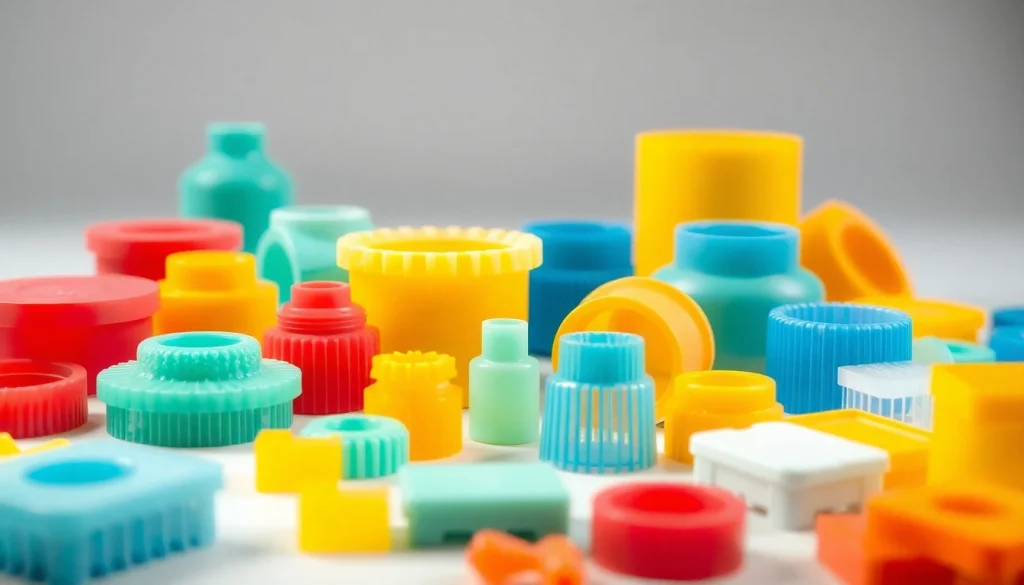
Understanding Blow Moulded Plastic Parts
Blow moulding is a widely utilized manufacturing process specifically designed to create hollow plastic parts. This innovative technique is indispensable for various industries, allowing for the efficient and cost-effective production of items ranging from plastic bottles to large containers. This article will explore the intricacies of blow moulded plastic parts, delve into the process of blow moulding, and highlight the numerous benefits these parts offer. Additionally, we will discuss the types and materials used in blow moulding, how to select the right supplier, recent innovations in the sector, and the challenges manufacturers face in production.
This in-depth examination aims to provide comprehensive insights into blow moulded plastic parts, presenting data-driven analysis and practical recommendations that can significantly benefit businesses interested in using this manufacturing process.
What are Blow Moulded Plastic Parts?
Blow moulded plastic parts are hollow components formed through a specialised process involving air pressure. The technique allows manufacturers to produce a variety of shapes and sizes by utilizing different mould configurations. This manufacturing process is pivotal for creating lightweight, durable items used in everyday applications, including automotive parts, packaging, and consumer goods.
Common examples of blow moulded plastic parts include:
- Containers and bottles for beverages and chemicals
- Automotive fuel tanks
- Office and home products like storage bins
- Hollow toys and sports equipment
The Blow Moulding Process Explained
The blow moulding process primarily consists of three main types: extrusion blow moulding, injection blow moulding, and injection stretch blow moulding. Each method has its distinct characteristics and applications.
1. Extrusion Blow Moulding
This method involves extruding a molten plastic parison, which is a tube-like structure, and placing it into a mould. The parison is then inflated using air pressure until it conforms to the shape of the mould. This technique is optimal for producing large parts like drums and containers and is often preferred for mass production due to its efficiency.
2. Injection Blow Moulding
In injection blow moulding, a preform (a solid plastic piece) is created using injection moulding. This preform is then heated and blown into the final shape. This method provides a more precision-oriented approach, suitable for small parts requiring high accuracy and excellent surface finish, such as bottles and jars.
3. Injection Stretch Blow Moulding
This method combines injection and blowing techniques, whereby the preform is stretched and then blown. It is particularly beneficial for producing stronger parts with enhanced durability. This method is frequently used for creating PET containers, which are commonly found in the beverage industry.
Benefits of Using Blow Moulded Parts
There are several reasons why businesses choose blow moulding when manufacturing plastic parts. Among them:
- Cost-Effectiveness: Blow moulding is an efficient process that reduces material wastage and increases production speed, leading to significant cost savings.
- Lightweight and Durable: The finished products are lightweight yet sturdy, making them ideal for various applications.
- Design Flexibility: Manufacturers can create complex shapes and sizes without significantly increasing production costs.
- High Production Rates: Blow moulding is capable of producing large volumes of parts in a relatively short time frame.
- Environmental Benefits: The process can utilize recycled materials, reducing the ecological footprint. Additionally, blow moulded items typically require less material than their injection-moulded counterparts.
Types of Blow Moulded Plastic Parts
Common Materials Used in Blow Moulding
The efficiency and versatility of blow moulding are partially attributed to the range of materials that can be utilized. The most common plastics employed include:
- Polyethylene (PE): Available in various densities (HDPE, LDPE, and LLDPE), it is widely used for its excellent chemical resistance and flexibility.
- Polypropylene (PP): Known for its toughness and resistance to fatigue, polypropylene is ideal for containers and automotive parts.
- Polyethylene Terephthalate (PET): Primarily used for beverage bottles, PET is appreciated for its clarity, strength, and recyclability.
- Polyvinyl Chloride (PVC): Utilized for its durability, PVC is often found in water containers and industrial applications.
- ABS (Acrylonitrile Butadiene Styrene): This material combines high impact resistance with strength, ideal for consumer products and parts in automotive manufacturing.
Applications Across Various Industries
Blow moulded plastic parts cater to an array of industries. Here are some key sectors that rely heavily on blow moulding:
- Packaging: Blow moulding is extensively used for packaging products, particularly beverages, cleaning supplies, and chemicals. The long shelf life and durability of blow moulded containers make them preferred choices.
- Automotive: The automotive industry utilizes blow moulding for manufacturing fuel tanks, dashboard components, and other hollow parts, enhancing overall vehicle performance.
- Consumer Goods: Products such as toys, storage containers, and sporting goods often leverage blow moulding for creating lightweight and durable items.
- Medical Devices: The regulatory standards and precision required in the medical field have led to the adoption of blow moulding for sterile packaging and disposable devices.
- Construction: Certain blow moulded parts are used in the construction sector for plumbing and electrical applications due to their strength and resistance to environmental factors.
Comparing Blow Moulded and Other Plastic Manufacturing Techniques
Blow moulding is one of several methods available for producing plastic parts. Others include injection moulding, rotational moulding, and thermoforming. Each technique offers unique advantages and is suited for different applications.
While injection moulding excels in producing solid parts with high precision, it tends to be more expensive and slower than blow moulding when it comes to creating hollow components. Rotational moulding is best for large, hollow items but involves longer production cycles and may lead to higher material waste. Thermoforming is suitable for flat or low-depth parts and is often less economically effective than blow moulding when hollow structures are required.
Choosing the Right Supplier for Blow Moulded Parts
Key Factors in Selecting a Supplier
Choosing the right supplier for blow moulded plastic parts is pivotal to ensuring product quality and production efficiency. Some critical factors to consider include:
- Experience and Expertise: Seek suppliers with a strong track record in blow moulding, as seasoned manufacturers are better equipped to handle complex projects.
- Technical Capabilities: Evaluate the supplier’s machinery and equipment to ensure they can meet your production requirements ranging from small to large volumes.
- Material Knowledge: Suppliers should be well-versed in the materials available for blow moulding and capable of advising which plastics best suit specific applications.
- Supply Chain Efficiency: Assess the supplier’s logistics capabilities to confirm they can deliver products on time and manage inventory effectively.
Evaluating Quality and Compliance
Quality assurance is paramount in blow moulding. Check that the potential supplier adheres to industry standards and certifications relevant to your sector, such as ISO 9001 or FDA regulations for medical devices. Conduct site visits or audits to observe their production processes and quality control measures, ensuring they maintain consistent quality throughout.
Understanding Supplier Capabilities
Before partnering with a supplier, ensure they can accommodate your manufacturing needs, including:
- Production Scale: Can they handle your batch sizes and fluctuating demands?
- Customization: Are they able to cater to unique designs or specifications?
- Post-Production Services: Do they offer support for assembly, packaging, or logistics?
Innovations in Blow Moulded Plastic Parts Manufacturing
Recent Technological Advances
The blow moulding industry has seen significant innovations in recent years, enhancing efficiency and product quality. Technological advancements include:
- Smart Manufacturing: Manufacturers are increasingly using IoT (Internet of Things) devices to monitor production processes, resulting in increased efficiency and reduced downtime.
- 3D Printing in Mould Design: The application of 3D printing technology can streamline the design and prototyping process, allowing for faster iterations of moulds.
- Advanced Robotics: Automation and robotics have made it possible to reduce human error and labour costs while increasing production speed and consistency.
Sustainability in Blow Moulding
Environmental sustainability is a growing concern across all industries, with blow moulding adapting to new practices that promote eco-friendliness. Some notable developments include:
- Use of Recycled Materials: Many manufacturers are shifting towards using recycled plastics to form blow moulded parts, reducing the reliance on virgin materials.
- Energy-Efficient Processes: Innovations in machinery and production techniques are continuously improving energy efficiency during the blow moulding process.
- Reduced Material Waste: Techniques such as optimising the parison design have been implemented to minimise the material used without compromising product quality.
Future Trends in the Industry
Looking ahead, the blow moulding industry is expected to evolve significantly, influenced by various trends including:
- Emphasis on Customisation: As consumer demands for unique and personalised products increase, blow moulding will adapt to offer greater options for custom shapes and designs.
- Digital Manufacturing: The shift towards digital and automated solutions will likely revolutionise blow moulding operations, enhancing efficiency and reducing costs.
- Focus on Biodegradable Plastics: The exploration of bio-based materials will gain traction, driven by the need for sustainable and environmentally-friendly manufacturing solutions.
Challenges in Blow Moulding Production
Common Issues Faced During Production
The blow moulding process, while efficient, is not without its challenges. Some common issues include:
- Defects in Moulding: Problems such as uneven wall thickness, which can lead to product failure, are often encountered.
- Material Selection: Choosing inappropriate materials can cause issues such as cracking or inadequate performance under pressure.
- Machine Downtime: Unscheduled breakdowns can disrupt production schedules, leading to increased costs and reduced output.
- Environmental Compliance: Adhering to environmental regulations can present challenges, particularly in managing waste and emissions.
How to Address Blow Moulding Challenges
Addressing these challenges requires a proactive approach, which can include:
- Regular Maintenance: Implementing a robust maintenance program can help prevent machine breakdowns and ensure consistent production.
- Enhanced Training: Providing comprehensive training for operators can increase awareness of potential issues and improve overall output quality.
- Investing in Technology: Upgrading to advanced blow moulding machines can reduce defects and improve the efficiency of the process.
- Rigorous Quality Control: Establishing a stringent quality management system can minimize defects and ensure consistent product standards.
Measuring Performance and Quality Control
Performance measurement is essential in blow moulding to ensure that production goals are met and that quality standards are maintained. Key performance indicators (KPIs) that should be monitored include:
- Production Rate: The number of parts produced over a specific time frame can indicate efficiency levels.
- Defect Rate: Tracking the percentage of defective products can help identify areas that require improvement.
- Material Utilisation: Evaluating how much of the material used results in saleable products can pinpoint wastage areas.
- Downtime: Monitoring downtime can help in identifying maintenance needs or production bottlenecks.