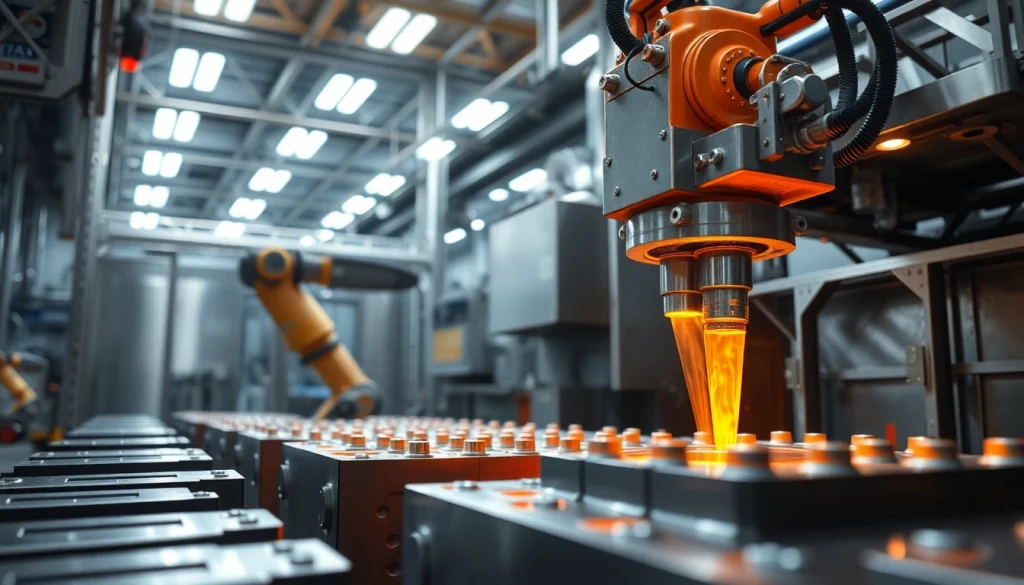
Introduction to the Manufacture of Plastic Parts
In today’s fast-paced industrial world, the manufacture of plastic parts has become an essential process across various sectors, such as automotive, aerospace, consumer goods, and healthcare. As a versatile and robust material, plastic offers numerous benefits, including lightweight properties, corrosion resistance, and the ability to be molded into complex shapes. Companies are increasingly turning to advanced manufacturing techniques to create high-quality plastic components that meet diverse needs.
Understanding Plastic Materials
Plastics can be broadly categorized into two main types: thermoplastics and thermosetting plastics. Thermoplastics are polymers that become moldable upon heating and solidify upon cooling, which allows for recycling and reshaping. Examples include polyethylene, polypropylene, and polyvinyl chloride (PVC). In contrast, thermosetting plastics undergo a chemical change when heated, creating a set shape that cannot be remolded. Common thermosetting plastics include epoxy and phenolic resins.
Why Choose Plastic Manufacturing?
Plastic manufacturing offers several advantages that make it a preferred choice for producing a variety of parts. Some key reasons include:
- Cost-effectiveness: Compared to metals, plastics are often less expensive to source and process.
- Design flexibility: The variety of plastic types and the ability to mold them into intricate shapes allows for innovative designs.
- Reduced weight: Plastics are typically lighter than metal, making them ideal for applications where weight is a concern.
- Corrosion resistance: Many plastics are resistant to moisture, chemicals, and UV radiation, enhancing their longevity in harsh environments.
- Energy efficiency: Many manufacturing processes for plastic use less energy compared to their metal counterparts.
Overview of Common Processes
The manufacture of plastic parts involves several key processes, including:
- Injection Molding: Widely used for mass production of items ranging from small components to large automotive parts.
- Extrusion: Useful for creating continuous profiles and shapes, such as tubes and pipes.
- Blow Molding: Ideal for hollow containers like bottles and tanks.
- Vacuum Forming: A technique for producing thin-walled parts by heating plastic sheets and forming them over molds.
- 3D Printing: An additive manufacturing technology that allows for rapid prototyping and customization.
Popular Manufacturing Techniques
Injection Molding: The Most Common Method
Injection molding is one of the most widely used methods in the manufacture of plastic parts, particularly for high-volume production. In this process, molten plastic is injected into a pre-designed mold, where it cools and solidifies into the final shape. This method is highly efficient and allows for the production of complex geometries with minimal waste.
Injection molding offers several advantages, including:
- High precision: Mold design can achieve tight tolerances, ensuring that parts fit together seamlessly.
- Speed: The cycle time can range from seconds to minutes, enabling rapid production.
- Repeatability: With automated processes, the quality and specifications remain consistent across all parts.
Exploring Extrusion Processes
Extrusion is another key method used in the manufacture of plastic parts. The process involves forcing melted plastic through a die to create continuous shapes, such as sheets, films, and various profiles. Extruded products can be cut to length and used in numerous applications, from construction materials to packaging.
One of the strengths of extrusion lies in its flexibility. Manufacturers can produce a wide range of products with varying dimensions and thicknesses, catering to specific industry needs. Additionally, the low-cost tooling compared to injection molding can make it a financially viable option for lower volume runs.
Alternative Techniques: Blow Molding and More
Blow molding is another popular technique, primarily used for creating hollow plastic parts, such as bottles and containers. This process involves inflating hot plastic within a mold to form the desired shape. The two main types of blow molding are extrusion blow molding and injection blow molding, each suited for different applications and material formulations.
Besides blow molding, there are several other techniques worth mentioning:
- Thermoforming: Using sheets of plastic, this method heats the material and forms it over a mold—commonly used for packaging and trays.
- Vacuum Casting: Allows for the production of small quantities of parts with high detail, typically for prototypes or small series production.
- Compression Molding: Suitable for thermosetting plastics, where preheated material is placed in a mold and compressed to achieve the desired form.
Choosing the Right Method for Your Project
Factors to Consider in Plastic Parts Manufacture
When selecting the appropriate manufacturing technique, several factors should be taken into account:
- Part design: The complexity and dimensions of the part can greatly influence the choice of process.
- Material properties: Different plastics have unique characteristics that may affect manufacturing, such as melting points and tensile strength.
- Production volume: High-volume production typically justifies the investment in injection molds, while lower volumes may favor extrusion or 3D printing.
- Lead time: Consider the urgency of the project; some processes yield faster results than others.
Cost Analysis of Different Techniques
Understanding the economics of each manufacturing process is critical for decision-making. While injection molding may have a higher initial setup cost due to mold production, it often results in lower costs per part for high-volume runs. Conversely, methods like 3D printing have minimal setup costs, ideal for prototyping and small batches but may incur higher costs per unit in larger quantities. A thorough cost analysis considering material, labor, tooling, and production time can help determine the most cost-effective solution for a specific project.
Case Studies of Successful Manufacturing
To illustrate the optimal application of these manufacturing processes, consider the following case studies:
- Automotive Industry: A leading automotive manufacturer successfully implemented injection molding to produce complex dashboard components, significantly reducing production time and cost while enhancing quality.
- Consumer Goods: A company specializing in kitchenware used blow molding to manufacture lightweight, durable bottles that meet consumer demand for both functionality and aesthetic appeal.
- Medical Devices: Utilizing thermoforming, a healthcare company designed cost-effective packaging solutions for medical supplies while maintaining compliance with strict industry standards.
Quality Control in the Manufacture of Plastic Parts
Essential Inspection Processes
Quality control is paramount in the manufacture of plastic parts to ensure that the final products meet the required specifications and standards. Essential inspection processes include:
- Incoming Material Inspection: Verify the quality of raw materials before they are used in production.
- In-Process Inspection: Monitor the production process for conformity to design specifications, including dimensions and tolerances.
- Final Product Inspection: Conduct thorough examinations of the finished parts, using methods such as visual checks, dimensional measurements, and functional testing.
Implementing Quality Management Systems
Implementing a robust quality management system (QMS) is crucial in the plastic manufacturing industry. A QMS guided by standards like ISO 9001 ensures a systematic approach to managing quality, promoting continuous improvement, and satisfying customer requirements. Key components of a successful QMS include:
- Document Control: Maintaining accurate records of processes, inspections, and quality metrics.
- Training Programs: Equipping employees with knowledge and skills pertaining to quality standards and inspection techniques.
- Corrective Actions: Establishing processes for addressing non-conformities and implementing corrective measures effectively.
Dealing with Common Manufacturing Defects
Manufacturing defects can significantly impact product performance and company reputation. Common issues include:
- Warpage: Can occur due to uneven cooling or improper mold design. Solutions include optimizing cooling rates and mold design adjustments.
- Surface Defects: Such as scratches or blemishes, can be minimized by maintaining mold cleanliness and conducting regular inspections.
- Dimensionally Out of Tolerance Parts: Can be tackled through regular calibration of machinery and strict adherence to set tolerances during production.
The Future of Plastic Manufacturing
Innovations in Plastic Manufacturing
The future of plastic manufacturing is bright, with technological advancements reshaping the industry landscape. Innovations such as automation, robotics, and artificial intelligence are streamlining operations, reducing human error, and enhancing productivity. Furthermore, additive manufacturing continues to gain traction, allowing for customization and rapid prototyping without the need for extensive tooling.
Sustainability Practices in the Industry
As environmental concerns grow, the plastic manufacturing industry is increasingly focusing on sustainability. Companies are exploring biodegradable plastics, recycling practices, and the reduction of waste in manufacturing processes. Initiatives to develop more sustainable materials and practices can help meet consumer demands while minimizing environmental impact.
Preparing for Industry 4.0
The rise of Industry 4.0, characterized by the integration of digital technologies into manufacturing, is transforming plastic production. Smart factories leverage data analytics, IoT devices, and automation to optimize processes, improve efficiencies, and predict maintenance needs. Embracing these technologies will be crucial for manufacturers aiming to stay competitive in a rapidly evolving market.