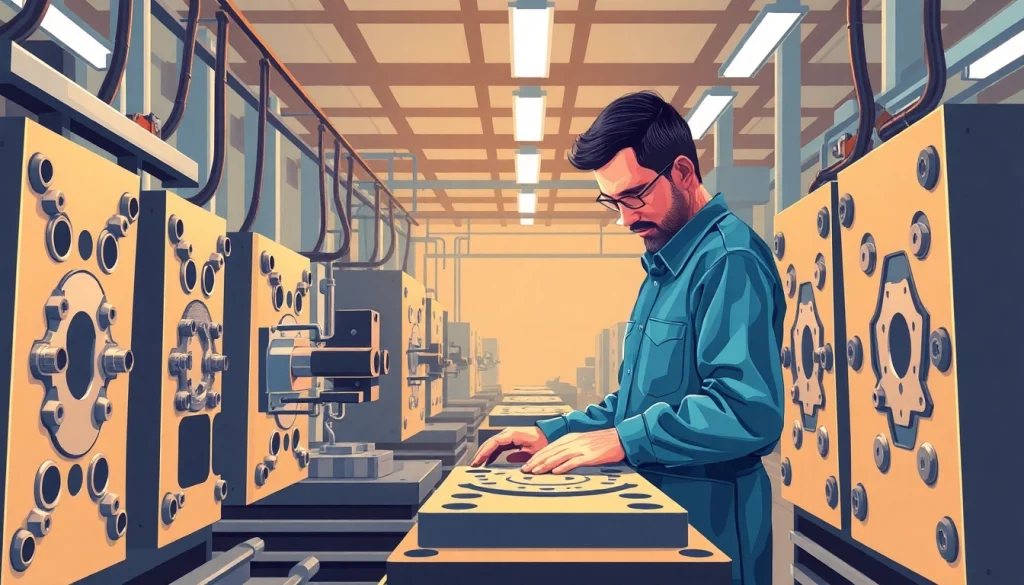
Understanding Injection Molding and Its Benefits
What is Injection Molding?
Injection molding is a modern manufacturing process for creating parts by injecting molten material into a mold. This technique is primarily used for plastics, but can also work with metals, glass, and ceramics. The process starts with a raw material that is heated until it becomes fluid. This fluid is then injected into a mold where it cools and solidifies into the desired product. The versatility and efficiency of injection molding make it a popular choice for large-scale manufacturing, allowing for the production of complex shapes with high precision.
Advantages of Injection Molding
Injection molding offers numerous advantages, including:
- Efficiency: The process can produce thousands of parts in a single cycle, significantly reducing production time and cost per unit.
- Consistency: Once a mold is created, each piece produced will have identical specifications, ensuring uniform quality.
- Material Variety: A wide range of materials can be used in injection molding, including thermoplastics, thermosets, and elastomers.
- Design Flexibility: Intricate and complex part designs can be achieved, providing freedom in product design and functionality.
- Low Scrap Rate: Compared to other manufacturing processes, injection molding produces less waste, as excess material can be recycled.
Common Applications of Injection Molding
Injection molding is used in multiple industries, such as:
- Automotive: Components like dashboards, bumpers, and interior trims.
- Consumer Electronics: Housings for devices like smartphones and computers.
- Medical Devices: Parts that require high precision, such as syringe bodies and catheter connectors.
- Household Goods: Utensils, furniture parts, and containers.
The Role of a Mold Maker in Injection Molding
What Does a Mold Maker Do?
A mold maker for injection molding is a specialized craftsman responsible for fabricating molds that are essential for the injection molding process. Mold makers design, build, and maintain the molds, ensuring they meet the precise specifications needed for quality production. Their work is vital, as the quality of the mold directly impacts the quality of the final products.
Skills and Qualifications of a Successful Mold Maker
To become an effective mold maker, individuals typically require a combination of technical skills, education, and experience. Common qualifications include:
- Technical Skills: Proficiency in machining, design software (like CAD), and an understanding of materials.
- Problem-Solving: The ability to diagnose and fix issues that may arise during the mold-making process.
- Attention to Detail: Precision is crucial in creating molds that fit perfectly and function reliably.
- Communication Skills: Effective collaboration with engineers and manufacturers is essential.
The Importance of Craftsmanship in Mold Making
Craftsmanship is paramount in mold making as it determines the mold’s durability, precision, and overall functionality. Skilled mold makers pay close attention to every detail, ensuring that even the smallest aspect of the mold is accounted for. This meticulous approach helps avoid costly mistakes and ensures the production of high-quality molded parts. Furthermore, as technology evolves, mold makers must adapt, continually refining their craft to incorporate new methods and tools into their work.
Choosing the Right Mold Maker for Injection Molding Projects
Key Factors to Consider When Selecting a Mold Maker
When looking for a mold maker for your injection molding projects, consider the following factors:
- Experience: Look for mold makers with a proven track record in your industry. Experience often correlates with expertise in handling complex designs and managing production challenges.
- Technology and Equipment: Ensure that the mold maker uses up-to-date technology and high-quality materials in their work.
- Reputation: Research past client testimonials and case studies to gauge reliable service and quality.
- Cost Structure: Understand the pricing model, and ensure it aligns with your budget while reflecting quality workmanship.
Top Questions to Ask Your Mold Maker
Before committing to a mold maker, consider asking:
- What is your experience with similar projects?
- Can you provide references from past clients?
- What is your typical lead time for mold fabrication?
- How do you ensure quality control throughout the mold-making process?
Evaluating the Experience and Expertise of Mold Makers
Evaluating a mold maker’s competence involves assessing their portfolio of previous work, certifications, and any industry-specific expertise. A good mold maker should be able to demonstrate flexibility in adapting to new projects and technologies while having a supportive team to back them up in complex projects.
Cost Considerations for Mold Making Services
Understanding the Cost Structure of Mold Making
The cost of mold making varies based on several factors, including mold complexity, size, and materials used. Generally, the cost can range widely from a few thousand to tens of thousands of dollars depending on the specifics of the project. For instance, simple molds can cost between $3,000 to $6,000, while complex, multi-cavity molds may start at $25,000 and rise into the six figures.
Factors Affecting Mold Making Costs
Several factors contribute to the overall cost of mold making, including:
- Mold Design: The intricacy of the mold design will significantly affect the cost. More features typically mean more machining time and complexity.
- Material Selection: The choice between different metals (e.g., aluminum vs. steel) can impact durability and cost.
- Production Volume: Higher production volumes may justify the higher upfront costs of a more durable mold.
Budgeting for Injection Molding Projects
When budgeting for mold making and injection molding projects, it is crucial to factor in all associated costs, such as design engineering, material costs, labor, and any potential revisions. Setting aside a contingency fund for unforeseen expenses can also help prevent budget overruns. Additionally, consider the long-term benefits of investing in high-quality molds, as they can lead to reduced production costs and waste in the long run.
Trends and Innovations in Mold Making for Injection Molding
Latest Technologies in Mold Production
The mold-making industry is continually evolving, integrating new technologies to enhance productivity and quality. Some of the latest trends include:
- 3D Printing: This technology allows for rapid prototyping and even direct mold production, reducing lead times and costs.
- Automated Machining: CNC (Computer Numerical Control) machining has revolutionized precision in mold making, allowing for highly intricate designs to be produced efficiently.
- Simulation Software: Tools that simulate the injection molding process can identify potential issues in mold design before production begins.
Sustainability Trends in Injection Molding
As industries become increasingly conscious of environmental issues, sustainability has taken center stage. Mold makers are focusing on:
- Eco-Friendly Materials: Using recycled and biodegradable materials in both mold making and production processes.
- Energy Efficiency: Enhancements in machinery and manufacturing processes to reduce energy consumption.
- Waste Reduction: Implementing processes to minimize waste and improve recyclability across the production line.
Future of Mold Making: What to Expect
The future of mold making points towards further integration of technology, with AI and machine learning likely playing increasing roles in optimizing designs and production processes. As manufacturers push towards leaner operations and enhanced quality, mold makers will adapt to provide innovative solutions that meet these rising demands. Improved collaboration with engineers and manufacturers will also be vital to creating molds that not only fulfill basic functional requirements but exceed expectations in durability and efficiency.