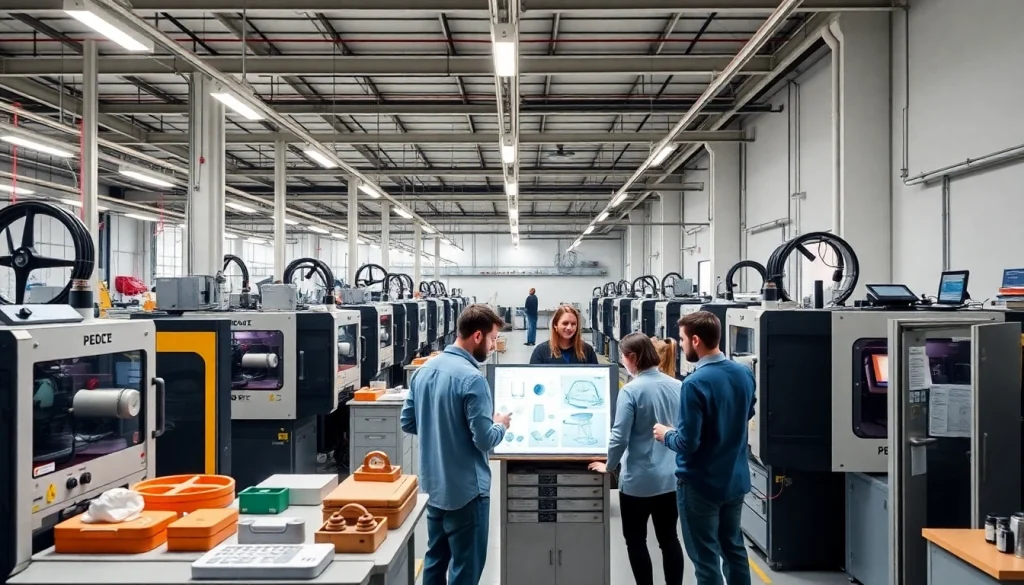
Understanding Injection Molding Services
Injection molding is a manufacturing process used for producing parts by injecting molten material into a mold. This method is particularly suited for high-volume production and is widely used in various industries, such as automotive, consumer products, and medical devices. Companies looking for reliable injection molding company must understand its fundamentals, capabilities, and advantages. This comprehensive guide will delve into various aspects of injection molding services, including its processes, benefits, and applications to empower companies to make informed decisions when selecting a partner in production.
What is Injection Molding?
Injection molding is a manufacturing process where molten plastic material is injected into a pre-designed mold cavity. The molded part cools and solidifies in the shape of the mold before being ejected. This process allows for the mass production of high-precision components and can handle several different thermoplastics and thermosetting polymers. Its main characteristics include:
- High Efficiency: Minimal manual intervention is required, leading to reduced labor costs.
- Repeatability: Once the mold is created, identical pieces can be mass-produced with high consistency.
- Design Flexibility: Complex shapes and designs can be achieved, making it suitable for diverse applications.
Types of Injection Molding Processes
There are several types of injection molding processes, each suitable for specific manufacturing needs. The most common include:
- Plastic Injection Molding: The most widely recognized type, it is used to create plastic parts. Various plastics can be utilized, including ABS, PS, and polycarbonate.
- Metal Injection Molding (MIM): A process that combines metal powders with a binding agent for producing small, complex parts.
- Insert Molding: The process involves placing a substrate within the mold before injecting the plastic, ensuring a strong bond between materials.
- Blow Molding: This involves creating hollow plastic containers and products, commonly used for bottles and packaging.
- Two-Shot Molding: It allows for the production of multi-material parts in one cycle, enhancing part functionality and aesthetics.
Benefits of Using an Injection Molding Company
Partnering with a dedicated injection molding company can provide numerous advantages, particularly for businesses aiming for efficiency and precision in their manufacturing efforts. Some of the key benefits include:
- Cost-Effectiveness: With high production volumes, the per-unit cost significantly decreases.
- Speed: The rapid cycle times of injection molding can lead to quicker product launches.
- Quality Control: Advanced technologies enable consistent quality checks throughout the manufacturing process.
- Customization: Tailored solutions can be developed based on specific industry needs, improving product functionality.
Choosing the Right Injection Molding Company
Selecting a reliable injection molding company is crucial for ensuring the quality, efficiency, and success of your manufacturing projects. Here are fundamental factors to consider when evaluating potential partners.
Assessing Quality Certifications
Quality certifications are critical indicators of an injection molding company’s operational standards. Companies should seek partnerships with manufacturers accredited by recognized organizations such as ISO 9001, ISO 13485, or TS16949. These certifications demonstrate a commitment to maintaining high-quality output and continuous improvement practices. Conducting thorough research on their compliance history offers insights into their reliability and quality assurance practices.
Evaluating Industry Experience
Experience in a specific industry can indicate a company’s ability to meet unique challenges and requirements. Companies should assess potential partners based on their historical performance in relevant sectors and the diversity of their served markets. A well-rounded injection molding company will be adept at understanding various applications, materials, and client expectations.
Comparing Costs and Services
Not all injection molding companies offer the same pricing structures or services. Businesses must compare multiple manufacturers based on their service offerings (including design assistance, prototyping, and production capabilities) and associated costs. It’s essential to consider not only the price but also the value provided, including services like after-sales support, tooling maintenance, and warranty options.
Innovations in Injection Molding
The injection molding industry continually evolves, integrating innovative technologies and practices to enhance efficiency and sustainability. Understanding these developments can help businesses stay competitive.
Technological Advances in the Industry
Recent technological advancements have significantly improved the injection molding process. Key innovations include:
- 3D Printing Integration: The inclusion of 3D printing in the design phase enables rapid prototyping, reducing time to market.
- Smart Manufacturing: IoT sensors are increasingly used to gather real-time data on machinery performance, allowing for better predictive maintenance and minimizing downtime.
- Advanced Materials: The availability of new, high-performance polymers expands the versatility of molded products, enabling engineers to meet stringent performance requirements.
Eco-Friendly Practices and Sustainability
With growing environmental concerns, many injection molding companies are adopting sustainable practices. These include:
- Recyclable Materials: Utilizing biodegradable and recyclable materials in the production process helps reduce waste and environmental impact.
- Energy-Efficient Equipment: Investing in energy-efficient machinery not only reduces energy consumption but also lowers operational costs.
- Closed-Loop Systems: Implementing systems that reuse and recycle scrap materials can enhance sustainability efforts.
Future Trends to Watch
As the industry advances, companies should keep an eye on future trends that may influence their operational strategies:
- Customization: The demand for tailored solutions will likely continue to grow, pushing manufacturers to innovate in their design and production processes.
- Digital Transformation: Continued investment in automation, AI, and machine learning will further streamline operations and enhance productivity.
- Increased Collaboration: Partnerships among technology providers, manufacturers, and clients will foster developments in new applications and materials.
Injection Molding Applications Across Industries
Injection molding is a crucial manufacturing process across various sectors. Here are some significant applications of injection molding and their impact on respective industries.
Aerospace and Automotive Uses
In the aerospace and automotive industries, injection molding is instrumental in producing lightweight yet durable components that are vital for efficiency and safety. Applications include:
- Structural components such as housing and panels that require high precision and reliability.
- Interior and exterior trims and fixtures that enhance aesthetics and functionality.
- Complex assemblies that combine multiple functionalities into one component, reducing assembly time.
Consumer Products and Packaging
From household items to robust packaging solutions, injection molding plays a pivotal role in the consumer goods sector. Typical applications cover:
- Durable products like toys, kitchen tools, and cleaning products made from various plastics that can withstand regular use.
- Packaging solutions such as containers and lids designed to be lightweight, yet sturdy to protect contents while minimizing waste.
- Innovative designs that cater to consumer demand for convenience and sustainability.
Medical Device Manufacturing
The medical device industry relies heavily on injection molding for producing precise and sterile components. Key areas of application include:
- Manufacturing critical parts like syringes, drug delivery devices, and surgical instruments.
- Creating custom components tailored to specific medical applications, enhancing patient care.
- Implementing strict quality control measures and compliant practices to meet regulatory standards.
Performance Metrics for Injection Molding
To evaluate the effectiveness of an injection molding operation, it’s essential to track specific performance metrics. These metrics help ensure quality and efficiency throughout the production process.
Understanding Production Volume and Cost
Production volume refers to the quantity of parts produced within a specific timeframe, while costs encompass all expenses related to production, including material, labor, and overhead. Businesses should examine:
- The relationship between production volume and cost, ensuring that increasing volumes lead to lowered per-unit costs.
- Monitoring changes in material costs and incorporating those adjustments into pricing strategies to maintain profitability.
- Analyzing cycle times to identify efficiencies or bottlenecks that could impact throughput.
Key Performance Indicators for Quality
Establishing KPIs for quality will help teams maintain high standards. Key indicators include:
- Defect rates, measured as the percentage of non-conforming parts produced.
- First-pass yield rates, which indicate the percentage of parts produced correctly on the first attempt.
- Overall equipment effectiveness (OEE), assessing the productivity and efficiency of machinery during production.
Evaluating Supplier Reliability and Lead Times
Supplier reliability and lead times significantly affect production schedules and inventory management. Companies should consider:
- Analyzing historical lead times to determine reliability and expected delivery standards.
- Assessing the impact of supplier delays on overall production timelines and planning accordingly.
- Building relationships with suppliers that provide consistent communication and visibility into their production processes.